Freeform Technologies
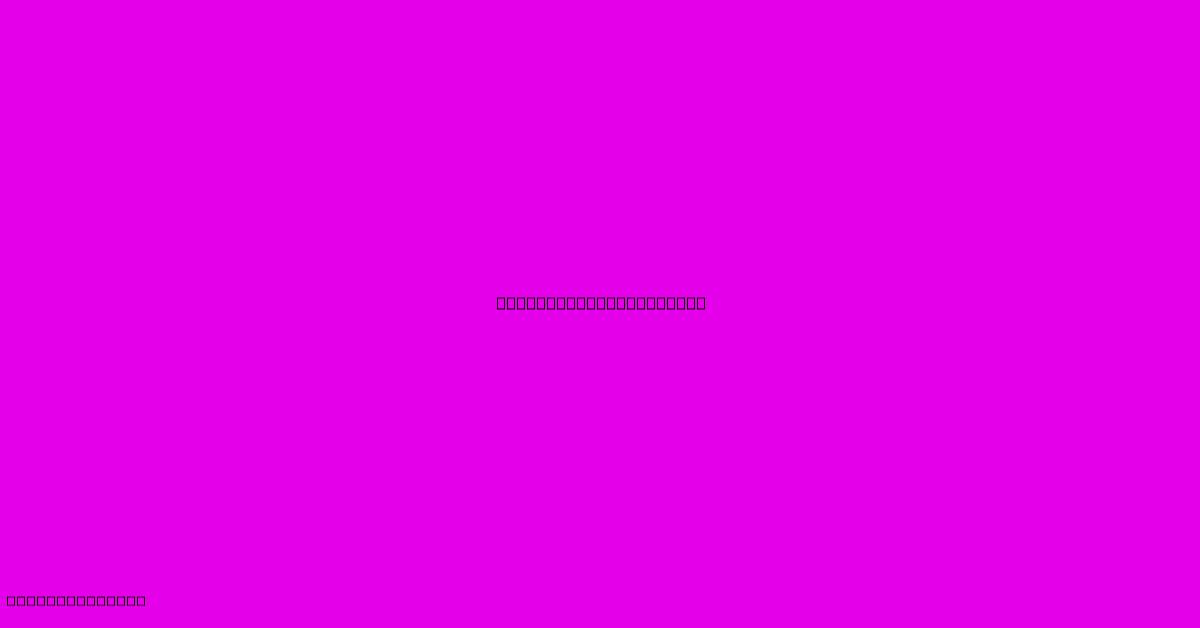
Discover more detailed and exciting information on our website. Click the link below to start your adventure: Visit Best Website mr.cleine.com. Don't miss out!
Table of Contents
Freeform Technologies: Shaping the Future of Manufacturing
Freeform technologies, also known as additive manufacturing or 3D printing, are revolutionizing the manufacturing landscape. They offer unparalleled design flexibility, faster prototyping, and on-demand production, impacting diverse sectors from aerospace to healthcare. This article delves into the core principles, advantages, limitations, and future trends of these transformative technologies.
What are Freeform Technologies?
Freeform technologies encompass a range of processes that build three-dimensional objects layer by layer from a digital design. Unlike traditional subtractive manufacturing (e.g., milling, turning), which removes material to create a part, additive manufacturing adds material to create the desired shape. This fundamental difference opens up a world of possibilities previously unattainable.
Several prominent freeform technologies exist, each with its strengths and weaknesses:
-
Stereolithography (SLA): Uses a laser to cure liquid resin, layer by layer, creating highly accurate and detailed parts. Ideal for prototypes and intricate designs.
-
Selective Laser Sintering (SLS): A powder-bed fusion technique that uses a laser to fuse powdered materials (plastics, metals, ceramics) together. Excellent for complex geometries and functional parts.
-
Fused Deposition Modeling (FDM): A widely accessible technology that extrudes molten thermoplastic filament to build objects. Relatively inexpensive but often with lower precision than other methods.
-
Direct Metal Laser Sintering (DMLS): Uses a high-powered laser to melt and fuse metal powders, ideal for creating strong and durable metal parts.
-
Electron Beam Melting (EBM): Similar to DMLS but uses an electron beam to melt metal powders in a vacuum. Produces high-density parts with excellent mechanical properties.
Advantages of Freeform Technologies:
The benefits of freeform technologies are substantial:
-
Design Flexibility: Create virtually any shape imaginable, including complex internal structures and geometries impossible with traditional methods.
-
Rapid Prototyping: Significantly reduces prototyping time and cost, allowing for quicker design iterations and faster product development cycles.
-
On-Demand Production: Manufacture parts only when needed, minimizing inventory costs and waste.
-
Customization: Easily produce customized products tailored to individual needs, enhancing personalization and value.
-
Lightweighting: Create lightweight components with optimized internal structures, improving performance and efficiency (especially crucial in aerospace and automotive).
-
Consolidation of Parts: Integrate multiple parts into a single unit, simplifying assembly and reducing production costs.
Limitations of Freeform Technologies:
Despite their advantages, several limitations remain:
-
Cost: Some freeform technologies, particularly those involving metal printing, can be expensive.
-
Build Time: Depending on the complexity and size of the part, the build time can be substantial.
-
Material Limitations: Not all materials are suitable for all freeform technologies.
-
Scalability: Scaling up production to meet high-volume demands can be challenging for some methods.
-
Post-Processing: Many freeform technologies require post-processing steps, such as cleaning, support structure removal, and finishing, adding to the overall production time.
Future Trends in Freeform Technologies:
The field of freeform technologies is constantly evolving. Key future trends include:
-
Multi-material printing: Combining different materials in a single part to optimize properties.
-
Increased automation: Developing more automated and streamlined workflows.
-
Improved materials: Expanding the range of printable materials, including biocompatible materials for biomedical applications.
-
Integration with AI and machine learning: Utilizing AI to optimize designs, predict material behavior, and improve process control.
-
Hybrid manufacturing: Combining additive and subtractive manufacturing processes to leverage the strengths of both.
Conclusion:
Freeform technologies are reshaping manufacturing by offering unprecedented design freedom, speed, and efficiency. While challenges remain, ongoing advancements promise to overcome these limitations, solidifying the role of additive manufacturing as a vital tool for innovation across numerous industries. The future of manufacturing is undoubtedly intertwined with the continued evolution and broader adoption of these powerful technologies.
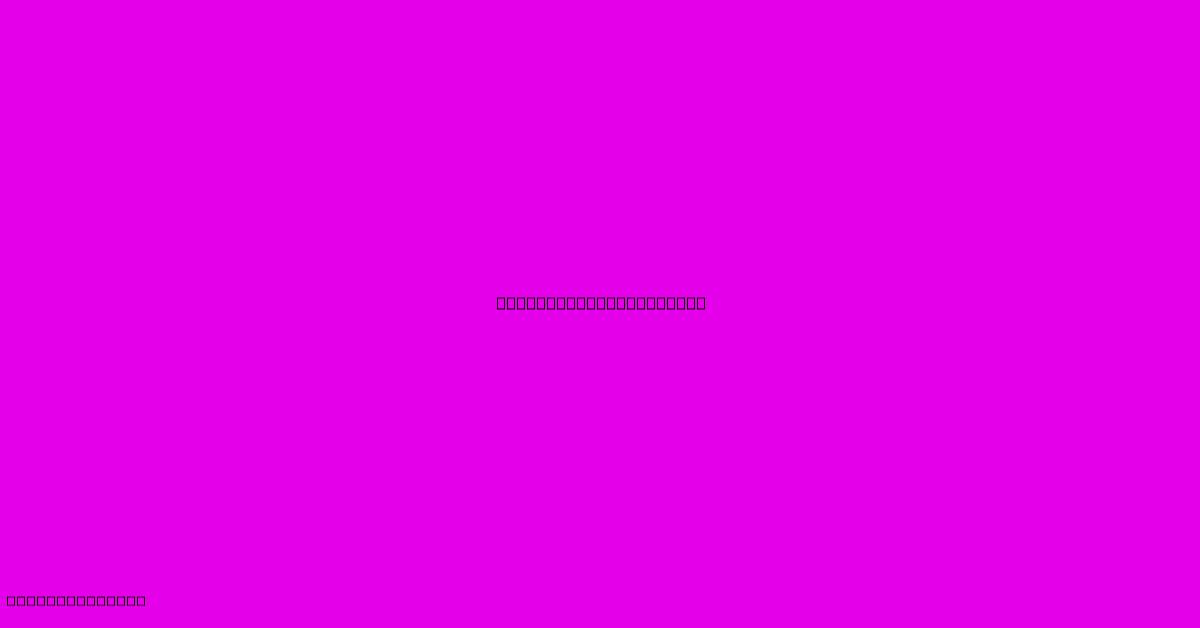
Thank you for visiting our website wich cover about Freeform Technologies. We hope the information provided has been useful to you. Feel free to contact us if you have any questions or need further assistance. See you next time and dont miss to bookmark.
Featured Posts
-
Persik Kediri Menang Dramatis
Dec 21, 2024
-
Petro Extrusion Technologies
Dec 21, 2024
-
Dell Technologies Class Action
Dec 21, 2024
-
Indoor Air Technologies
Dec 21, 2024
-
Bayrou Et Le Gouvernement Avis De Bardella
Dec 21, 2024