Forming Technologies
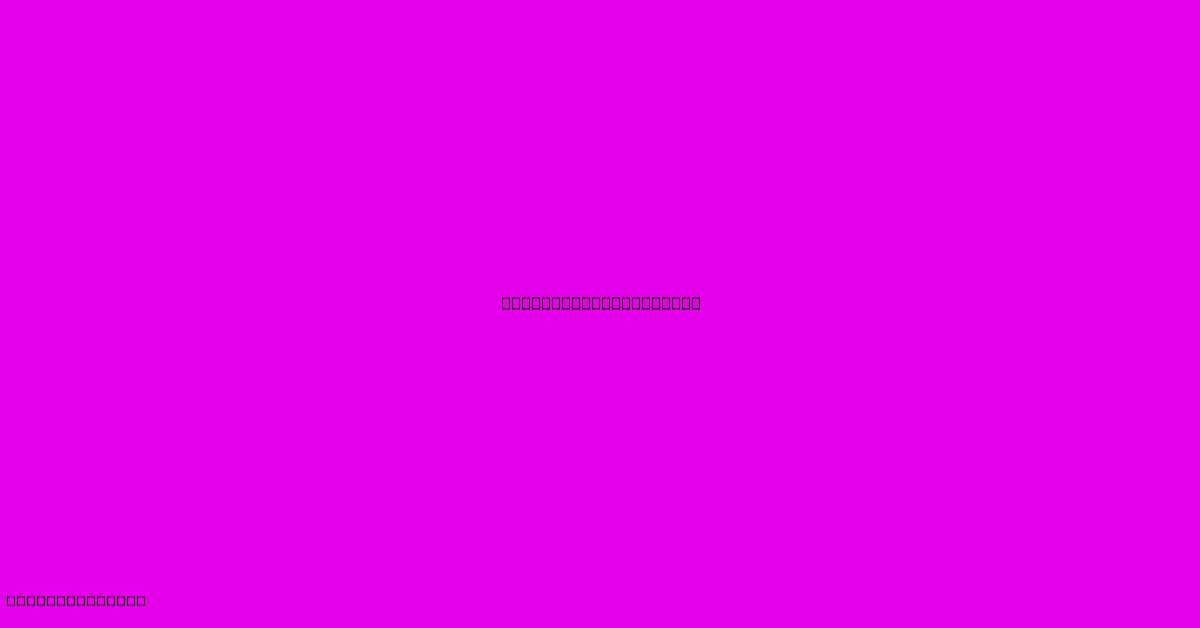
Discover more detailed and exciting information on our website. Click the link below to start your adventure: Visit Best Website mr.cleine.com. Don't miss out!
Table of Contents
Forming Technologies: Shaping the Future of Manufacturing
Forming technologies are essential processes in manufacturing, enabling the creation of complex shapes from various materials. These techniques are crucial across numerous industries, from automotive and aerospace to consumer goods and medical devices. This article delves into the diverse world of forming technologies, exploring their principles, applications, and the ongoing innovations shaping their future.
Understanding the Fundamentals of Forming
Forming, also known as metal forming or material forming, encompasses a broad range of processes that permanently alter the shape of a material without removing any material. Unlike machining, which subtracts material, forming utilizes pressure and deformation to achieve the desired geometry. This makes it a highly efficient and often cost-effective manufacturing approach.
Major Categories of Forming Technologies:
Several distinct categories exist within the realm of forming technologies, each employing unique methods and suitable for different materials and applications:
1. Bulk Forming: These processes involve significant deformation of large volumes of material. Key examples include:
- Forging: A powerful technique involving hammering or pressing heated metal into a desired shape. This results in high strength and durability. Variations include open-die forging, closed-die forging, and press forging.
- Rolling: A continuous process used to reduce the thickness of metal sheets or create profiles like bars and rods. The material is passed through a series of rollers, progressively shaping it.
- Extrusion: Pushing a heated material through a die to create a continuous profile, such as pipes, rods, or complex shapes.
2. Sheet Metal Forming: This focuses on shaping thin metal sheets, offering versatility in design and production. Common methods include:
- Stamping: Using dies to punch, bend, or form shapes from sheet metal. This is a high-volume production method, widely used in automotive and electronics manufacturing.
- Bending: Deforming sheet metal by applying force to create angles or curves. Various bending techniques exist, adapted to different material thicknesses and radii.
- Drawing: Pulling a sheet metal blank through a die to create a cup or similar shape. This is commonly used in the production of containers and automotive parts.
- Spinning: Rotating a metal blank while a tool shapes it against a mandrel, creating axisymmetric parts.
3. Powder Metallurgy: This innovative technique involves compacting metal powders into a desired shape and then sintering (heating) them to bond the particles. It's ideal for creating complex geometries and components with unique properties.
4. Superplastic Forming: This process utilizes the superplastic behavior of certain materials at elevated temperatures to enable substantial deformation with minimal cracking. It is especially valuable for lightweight and high-strength components.
Material Considerations:
The choice of forming technology depends heavily on the material being processed. Factors such as ductility, strength, and temperature sensitivity significantly influence the feasibility and efficiency of different forming processes. Metals like steel, aluminum, titanium, and various alloys are commonly formed. However, polymers and composites are also increasingly utilized in forming technologies.
Advantages and Disadvantages of Forming Technologies:
Advantages:
- High production rates (especially for stamping and rolling)
- Excellent strength and dimensional accuracy in many cases
- Material conservation (minimal waste compared to machining)
- Capability to create complex shapes
- Cost-effectiveness (especially for high-volume production)
Disadvantages:
- High initial investment in tooling (dies, presses, etc.)
- Limited design flexibility in some processes
- Potential for surface defects or internal stresses
- Material limitations (not all materials are suitable for all forming processes)
Future Trends in Forming Technologies:
The field of forming is constantly evolving, driven by advancements in materials science, computer-aided design (CAD), and manufacturing automation. Key trends include:
- Simulation and Modeling: Advanced computer simulations allow for the optimization of forming processes and the prediction of material behavior, leading to improved efficiency and reduced defects.
- Automation and Robotics: Robots are increasingly integrated into forming operations, enhancing productivity, precision, and safety.
- Additive Manufacturing Integration: Combining additive manufacturing (3D printing) with forming technologies allows for the creation of highly customized and complex components.
- New Materials and Alloys: The development of new materials with improved formability is driving innovation in forming processes.
- Sustainable Practices: The emphasis on sustainable manufacturing is pushing the adoption of environmentally friendly forming techniques and materials.
Conclusion:
Forming technologies play a pivotal role in modern manufacturing, offering efficient and versatile methods for creating a wide range of parts and products. The ongoing advancements in this field promise even greater capabilities in the future, driving progress across multiple industries. Understanding the fundamentals and trends in forming technologies is crucial for anyone involved in the design, manufacture, and application of materials.
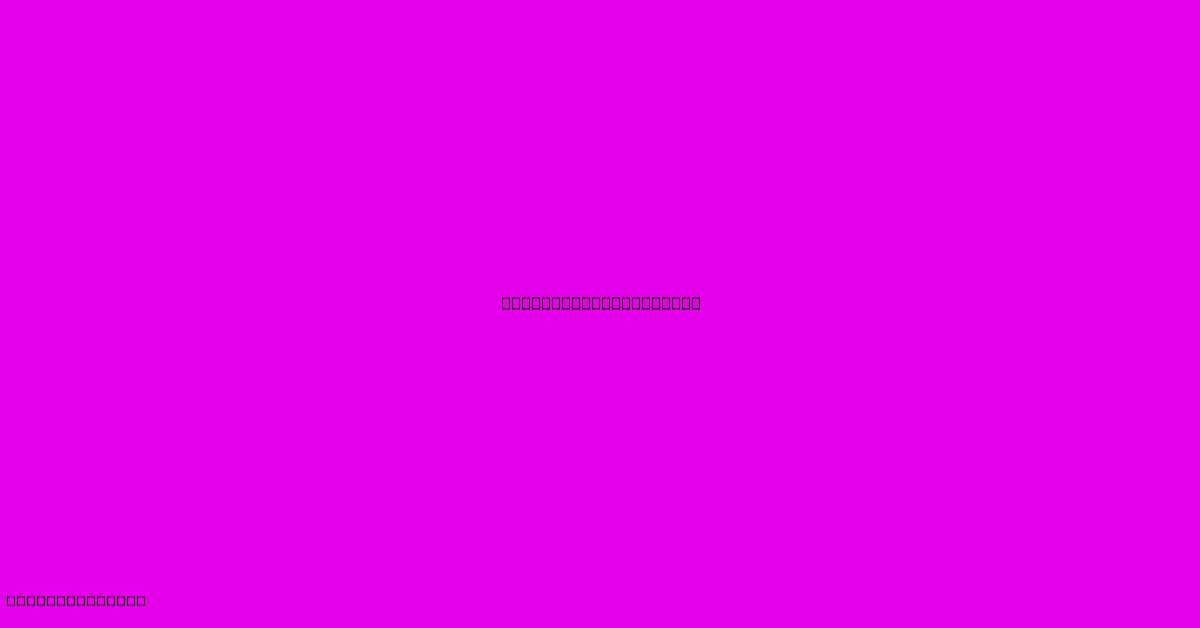
Thank you for visiting our website wich cover about Forming Technologies. We hope the information provided has been useful to you. Feel free to contact us if you have any questions or need further assistance. See you next time and dont miss to bookmark.
Featured Posts
-
M7 Technologies
Jan 03, 2025
-
An Intelligent Workplace Uses Technology To Enable Workers
Jan 03, 2025
-
Riverside Institute Of Technology
Jan 03, 2025
-
Indus Valley Technology
Jan 03, 2025
-
Information Technology Jobs Phoenix
Jan 03, 2025