Fluid Line Technology
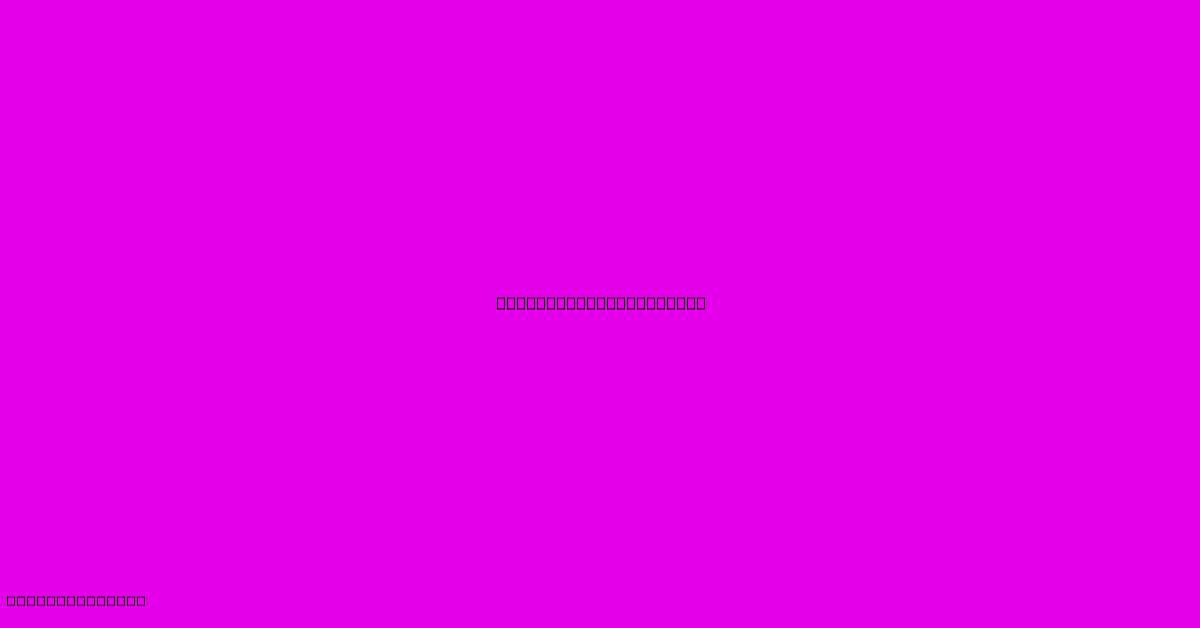
Discover more detailed and exciting information on our website. Click the link below to start your adventure: Visit Best Website mr.cleine.com. Don't miss out!
Table of Contents
Fluid Line Technology: Revolutionizing Design and Manufacturing
Fluid Line Technology, also known as fluidic line technology or freeform fabrication, represents a significant advancement in manufacturing and design. It leverages the principles of fluid dynamics and advanced materials to create complex, aesthetically pleasing, and structurally efficient shapes previously impossible using traditional methods. This article will delve into the core concepts, applications, and future prospects of this groundbreaking technology.
What is Fluid Line Technology?
Fluid Line Technology departs from conventional subtractive or additive manufacturing processes. Instead of carving away material or layering it incrementally, this approach uses a continuous flow of material – often a resin or polymer – that is guided and shaped by precisely controlled forces. These forces can include:
- Pressure: Regulating the pressure of the fluid material dictates the thickness and flow rate.
- Magnetic Fields: Used to manipulate the flow of magnetically sensitive fluids, allowing for intricate shaping.
- Electric Fields: Similar to magnetic fields, electric fields can be used to influence the movement of electrically conductive fluids.
- 3D-Printed Molds: These molds serve as guides, shaping the flowing material into the desired form.
The resulting products are characterized by smooth, flowing lines and curves, often mimicking organic forms found in nature. This contrasts sharply with the sharp edges and angles typical of traditional manufacturing.
Advantages of Fluid Line Technology
Several key advantages propel Fluid Line Technology to the forefront of innovative manufacturing:
- Design Flexibility: The ability to create intricate, freeform shapes opens up unprecedented possibilities for designers. This offers greater freedom to explore complex geometries and organic forms.
- Lightweight Structures: By precisely controlling material distribution, fluid line processes can create structures that are both strong and lightweight, minimizing material waste and improving efficiency.
- Improved Efficiency: The continuous flow of material reduces the need for multiple manufacturing steps, resulting in faster production times and potentially lower costs.
- Enhanced Aesthetics: The smooth, flowing lines and organic forms produced create aesthetically pleasing products, adding a unique visual appeal.
- Material Versatility: While currently focused on resins and polymers, the technology holds potential for use with other materials, expanding its applications further.
Applications of Fluid Line Technology
The versatility of Fluid Line Technology is reflected in its diverse applications across various industries:
- Automotive: Creating lightweight and aerodynamic body parts, interior components, and even entire car chassis.
- Aerospace: Designing and manufacturing lightweight and strong aircraft components, reducing fuel consumption and improving flight performance.
- Consumer Products: Producing sleek and aesthetically pleasing electronics housings, furniture, and other consumer goods.
- Medical Devices: Creating custom-designed prosthetics, implants, and surgical instruments.
- Architecture: Constructing complex and aesthetically pleasing building structures, reducing material usage and environmental impact.
Challenges and Future Directions
Despite its advantages, Fluid Line Technology faces several challenges:
- Material Limitations: Current processes are mostly limited to specific materials, restricting applications. Research is ongoing to expand compatible materials.
- Scaling Up Production: Transitioning from laboratory-scale prototypes to mass production remains a significant hurdle.
- Cost-Effectiveness: While the technology offers long-term cost savings, initial investment can be high.
The future of Fluid Line Technology appears bright. Ongoing research focuses on:
- Expanding Material Compatibility: Developing processes for a wider range of materials, including metals and composites.
- Improving Precision and Control: Refining the processes to achieve even greater accuracy and control over the final shape.
- Developing More Efficient Manufacturing Processes: Optimizing the technology for mass production, reducing costs, and increasing efficiency.
In conclusion, Fluid Line Technology is poised to revolutionize design and manufacturing, offering unprecedented freedom in creating innovative and sustainable products. As research progresses and the technology matures, its impact across diverse sectors will undoubtedly increase.
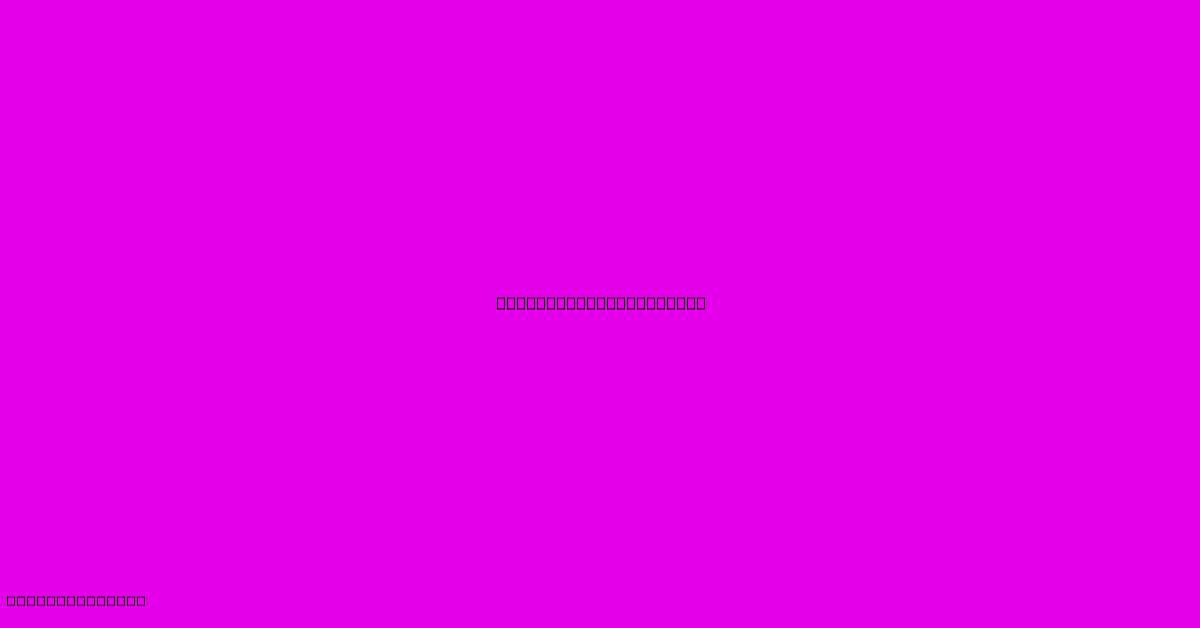
Thank you for visiting our website wich cover about Fluid Line Technology. We hope the information provided has been useful to you. Feel free to contact us if you have any questions or need further assistance. See you next time and dont miss to bookmark.
Featured Posts
-
Wcpss Technology Minecraft
Dec 23, 2024
-
Xem Truc Tiep Mu Vs Bournemouth
Dec 23, 2024
-
Svolt Energy Technology Co
Dec 23, 2024
-
Spurs Vs Liverpool Full Team Lineups
Dec 23, 2024
-
Patriots Vs Bills Week 16 Live
Dec 23, 2024