Flexo Technologies
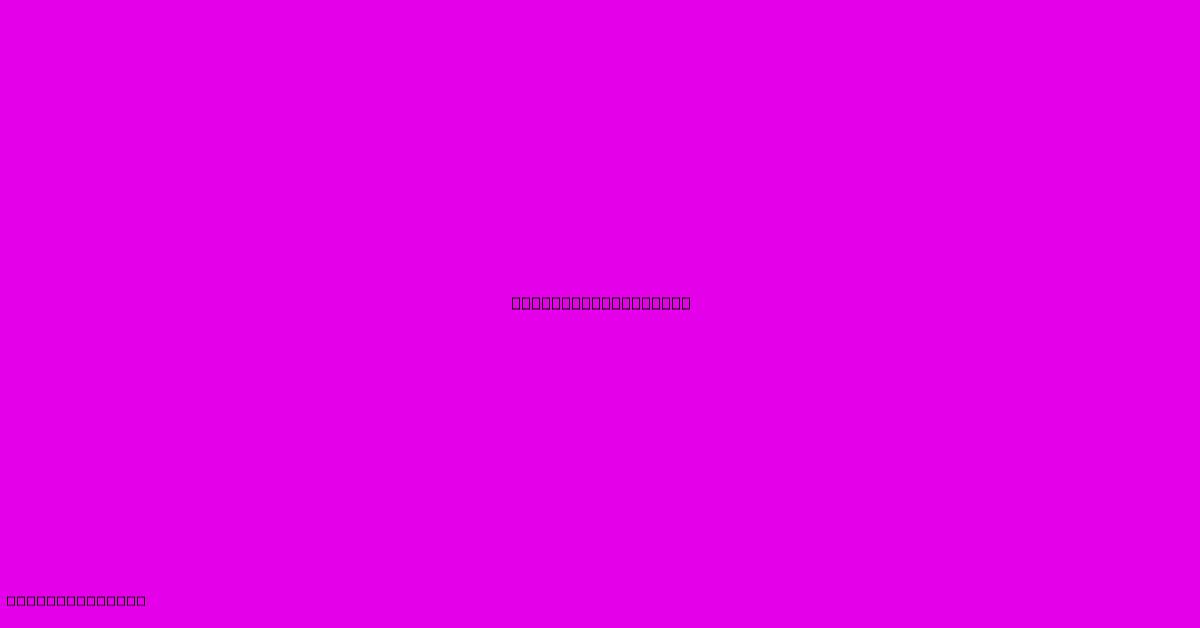
Discover more detailed and exciting information on our website. Click the link below to start your adventure: Visit Best Website mr.cleine.com. Don't miss out!
Table of Contents
Flexo Printing Technologies: A Deep Dive into Modern Printing
Flexographic printing, often shortened to flexo, is a versatile and widely used printing process that employs flexible, photopolymer plates to transfer ink onto a variety of substrates. This method boasts impressive speed, cost-effectiveness, and adaptability, making it a dominant force in packaging, labels, and other high-volume printing applications. Let's explore the intricacies of flexo technologies and what makes them so impactful.
Understanding the Flexo Printing Process
At its core, flexo printing involves transferring ink from a raised image area on a flexible plate to a substrate. This contrasts with other printing methods like offset lithography, which uses a flat plate and a complex inking system. The key components of the flexo process include:
-
Flexible Plates: These are typically made from photopolymer materials, which are light-sensitive and can be precisely etched to create the desired image. The flexibility allows the plates to conform to various substrate surfaces.
-
Ink: Flexographic inks are formulated for fast drying and excellent adhesion to different materials, including paper, film, foil, and corrugated board. Water-based, UV-curable, and solvent-based inks are commonly employed.
-
Anilox Roll: This crucial component meters the ink evenly onto the printing plate. The anilox roll has a finely etched surface with thousands of tiny cells, ensuring consistent ink transfer.
-
Printing Press: Flexo presses are designed to handle high speeds and various substrate widths. They incorporate sophisticated controls to manage ink density, register, and web tension.
Advantages of Flexo Printing Technologies
The popularity of flexo printing stems from its numerous advantages:
-
High Speed and Efficiency: Flexo presses can achieve exceptionally high printing speeds, ideal for large-volume production runs. This translates to lower per-unit costs.
-
Versatile Substrates: The process can print on a wide range of materials, from thin films to thick corrugated board, offering immense flexibility in applications.
-
Cost-Effective: Compared to other printing methods, flexo printing generally offers a lower cost per unit, particularly for large runs. Plate costs are also relatively low.
-
High-Quality Printing: Modern flexographic technologies produce high-quality prints with vibrant colors and sharp details. Advances in plate-making and ink technologies have significantly improved print resolution.
-
Environmentally Friendly Options: The availability of water-based and UV-curable inks contributes to environmentally conscious printing practices, minimizing volatile organic compound (VOC) emissions.
Modern Advancements in Flexo Technologies
The flexo printing industry is constantly evolving. Key innovations driving its progress include:
-
Digital Flexo: This technology eliminates the need for traditional platemaking, allowing for on-demand printing and reduced setup times. Digital flexo opens doors for short-run and personalized printing.
-
HD Flexo: High-definition flexo utilizes advanced plate-making techniques and enhanced screening methods to achieve significantly higher print resolution, resulting in sharper images and finer details.
-
Narrow Web Flexo: Narrow web flexo presses are designed for smaller-width substrates, ideal for label printing and other specialized applications.
-
Automation and Process Control: Increased automation and sophisticated controls improve consistency and reduce operator intervention, boosting productivity and reducing errors.
Applications of Flexo Printing
Flexo printing finds applications in a multitude of industries:
-
Packaging: This is the most prevalent application, encompassing food packaging, consumer goods packaging, and industrial packaging.
-
Labels: Flexo is extensively used for producing labels for various products, from food and beverages to cosmetics and pharmaceuticals.
-
Corrugated Board: The process is well-suited for printing on corrugated board used in shipping cartons and displays.
-
Flexible Packaging: Pouches, films, and other flexible packaging materials often utilize flexo printing for their vibrant designs.
Conclusion
Flexographic printing technologies continue to be a cornerstone of the printing industry, offering speed, versatility, and cost-effectiveness. As innovations like HD flexo and digital flexo continue to develop, this printing method will remain a vital part of the packaging, labeling, and broader printing landscape for years to come. The ongoing refinements in ink chemistry, plate-making, and press automation will ensure its continued relevance and adaptability to ever-evolving market demands.
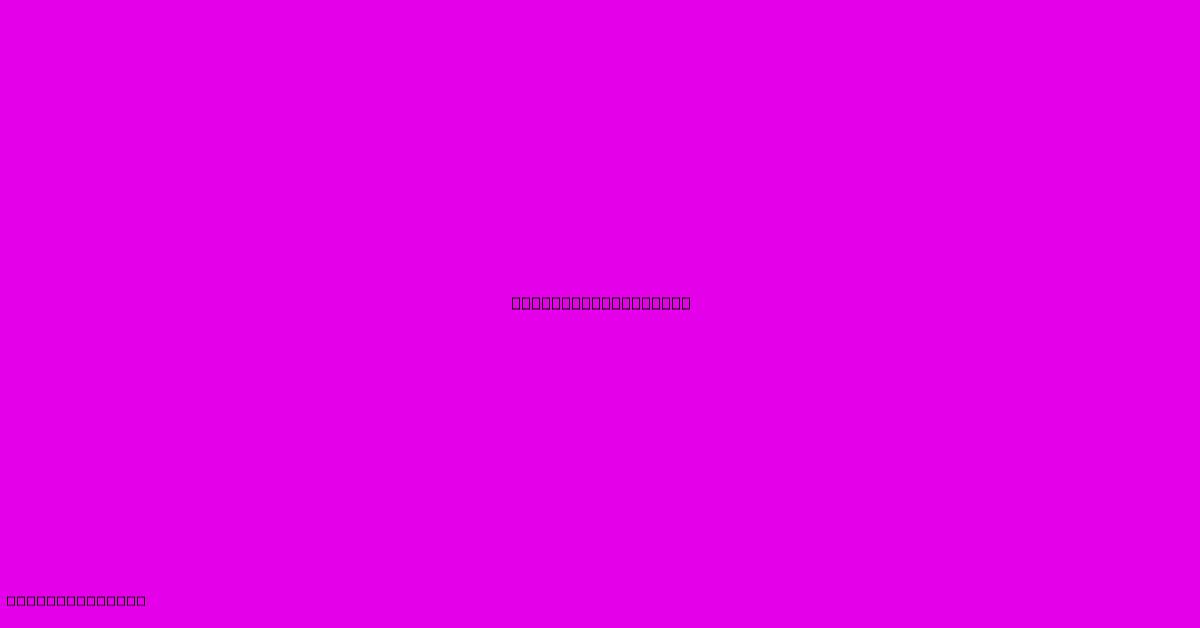
Thank you for visiting our website wich cover about Flexo Technologies. We hope the information provided has been useful to you. Feel free to contact us if you have any questions or need further assistance. See you next time and dont miss to bookmark.
Featured Posts
-
Meadowgate Technologies
Jan 03, 2025
-
Mechanical Technologies Reviews
Jan 03, 2025
-
Interglobe Technologies News
Jan 03, 2025
-
Clean Skies Technologies Reviews
Jan 03, 2025
-
Roper Technologies Careers
Jan 03, 2025