Dmc Technology
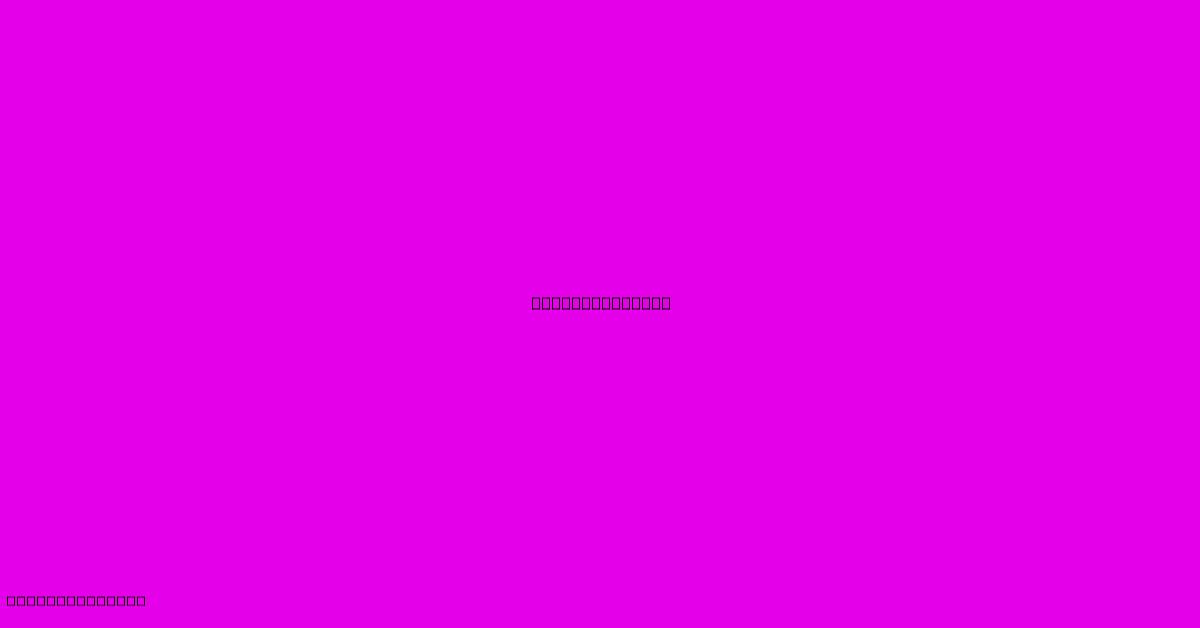
Discover more detailed and exciting information on our website. Click the link below to start your adventure: Visit Best Website mr.cleine.com. Don't miss out!
Table of Contents
Demystifying DMC Technology: A Deep Dive into Digital Manufacturing Capabilities
Keywords: DMC Technology, Digital Manufacturing, Manufacturing Execution Systems (MES), Industrial IoT (IIoT), Smart Manufacturing, Data Analytics, Predictive Maintenance, Production Optimization, Supply Chain Management, Digital Twin
The manufacturing landscape is undergoing a seismic shift, driven by the relentless pursuit of efficiency, agility, and innovation. At the heart of this transformation lies DMC Technology, or Digital Manufacturing Cloud technology. It's more than just a buzzword; it represents a fundamental change in how products are designed, manufactured, and delivered. This article delves into the core components, benefits, and challenges of adopting DMC technology.
What is DMC Technology?
DMC technology leverages cloud computing, advanced analytics, and the Industrial Internet of Things (IIoT) to create a fully connected and intelligent manufacturing ecosystem. It encompasses a broad range of technologies, working together to optimize every stage of the production lifecycle. Think of it as a central nervous system for your factory, providing real-time visibility, predictive capabilities, and data-driven decision-making.
Key Components of DMC Technology:
-
Manufacturing Execution Systems (MES): The backbone of DMC, MES provides real-time monitoring and control of manufacturing operations. It integrates data from various sources, including machines, sensors, and ERP systems, providing a unified view of production.
-
Industrial Internet of Things (IIoT): IIoT devices (sensors, actuators, etc.) embedded in machinery and throughout the factory floor collect vast amounts of data on equipment performance, product quality, and environmental conditions. This data fuels the intelligence of the DMC.
-
Data Analytics and Machine Learning: Advanced analytics algorithms process the IIoT data to identify trends, anomalies, and areas for improvement. Machine learning helps predict equipment failures, optimize production parameters, and enhance quality control.
-
Cloud Computing: The cloud serves as the central repository for all the data generated by the DMC. This allows for scalable storage, easy access to information, and collaborative workflows across different locations and teams.
-
Digital Twin Technology: A virtual representation of the physical manufacturing process, the digital twin allows for simulations, optimization testing, and predictive maintenance.
Benefits of Implementing DMC Technology:
-
Increased Efficiency: Real-time monitoring and optimization lead to reduced downtime, improved throughput, and faster production cycles.
-
Enhanced Quality: Data-driven insights enable proactive identification and correction of quality issues, leading to fewer defects and higher customer satisfaction.
-
Improved Productivity: Optimized workflows, reduced waste, and predictive maintenance contribute to significantly higher overall equipment effectiveness (OEE).
-
Reduced Costs: Lower downtime, reduced waste, and optimized resource allocation translate to significant cost savings.
-
Greater Agility: DMC enables faster response to market changes and customer demands through flexible manufacturing processes.
-
Better Decision-Making: Data-driven insights empower informed decisions across all aspects of manufacturing, from planning to execution.
Challenges of Adopting DMC Technology:
-
High Initial Investment: Implementing DMC requires significant upfront investment in hardware, software, and integration services.
-
Data Security and Privacy: Protecting sensitive manufacturing data from cyber threats is crucial.
-
Integration Complexity: Integrating disparate systems and data sources can be challenging and time-consuming.
-
Skills Gap: Organizations need skilled personnel to manage and interpret the vast amounts of data generated by DMC.
-
Change Management: Successfully implementing DMC requires a cultural shift within the organization, embracing new technologies and processes.
Conclusion:
DMC technology is transforming the manufacturing industry, offering unprecedented levels of efficiency, agility, and innovation. While the initial investment and integration complexities can be daunting, the long-term benefits significantly outweigh the challenges. Companies that embrace DMC technology will be well-positioned to thrive in the increasingly competitive global market. The journey toward a truly digital manufacturing enterprise requires careful planning, strategic investment, and a commitment to continuous improvement.
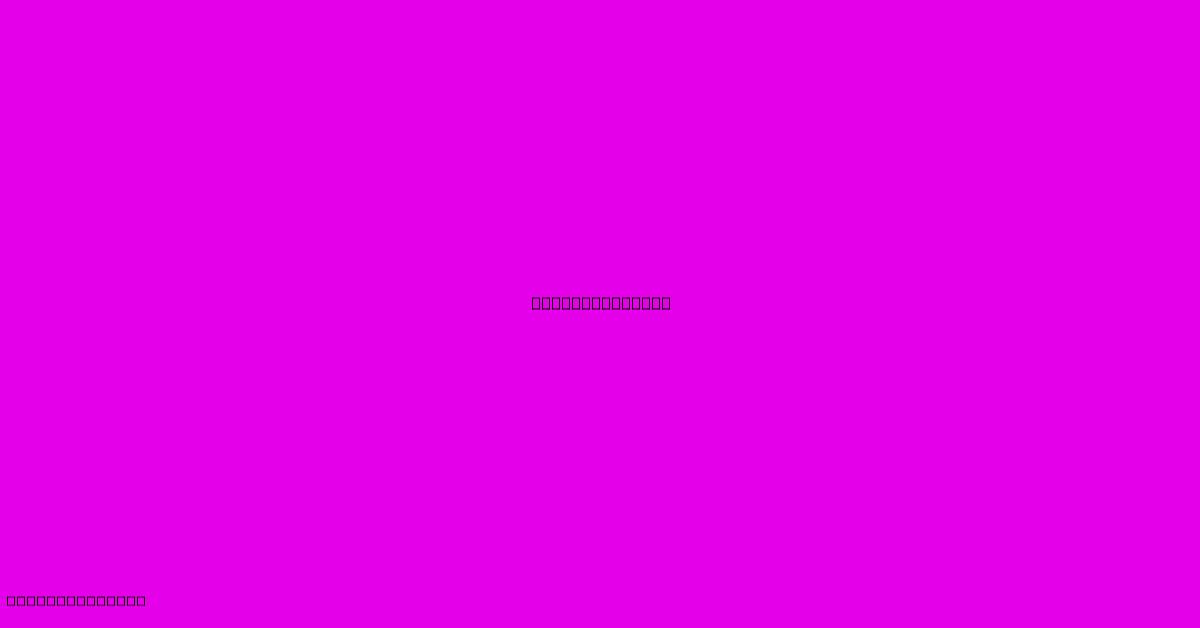
Thank you for visiting our website wich cover about Dmc Technology. We hope the information provided has been useful to you. Feel free to contact us if you have any questions or need further assistance. See you next time and dont miss to bookmark.
Featured Posts
-
Edm Technologies
Dec 21, 2024
-
Qmc Technologies
Dec 21, 2024
-
Usyk Vs Fury 2 Diffusion Tv
Dec 21, 2024
-
Blockchain Technology Reduces Fraud And Improves Efficiency
Dec 21, 2024
-
2019 Technology Way Green Bay
Dec 21, 2024