Dimension Technology
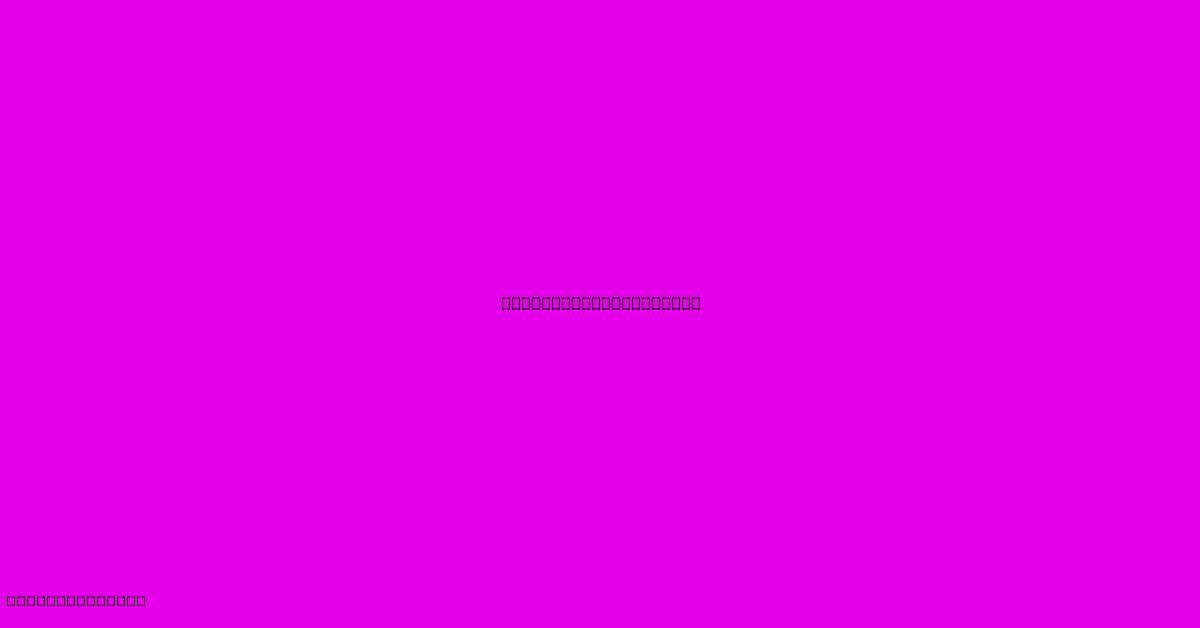
Discover more detailed and exciting information on our website. Click the link below to start your adventure: Visit Best Website mr.cleine.com. Don't miss out!
Table of Contents
Delving into the World of Dimension Technology: Beyond the Hype
Dimension technology, a term often tossed around in discussions about advanced manufacturing and design, encompasses a range of techniques and processes that create three-dimensional objects from digital models. While the term itself is broad, it primarily refers to additive manufacturing (also known as 3D printing) and subtractive manufacturing techniques that leverage advanced digital design and control systems. This article will explore the key aspects of dimension technology, its applications, advantages, limitations, and future prospects.
What is Dimension Technology?
At its core, dimension technology bridges the gap between the digital world and the physical realm. It allows designers and engineers to translate their computer-aided designs (CAD) into tangible objects with unprecedented precision and complexity. This capability revolutionizes various industries by enabling rapid prototyping, customized production, and the creation of intricate designs that would be impossible using traditional methods.
Key Processes within Dimension Technology:
Several core processes fall under the umbrella of dimension technology:
-
Additive Manufacturing (3D Printing): This is arguably the most well-known aspect of dimension technology. It involves building a three-dimensional object layer by layer from a digital model. Various techniques exist, including:
- Fused Deposition Modeling (FDM): Melts and extrudes thermoplastic filament to create the object.
- Stereolithography (SLA): Uses a laser to cure liquid resin, solidifying it layer by layer.
- Selective Laser Sintering (SLS): Uses a laser to fuse powdered material, creating a solid object.
- Multi Jet Fusion (MJF): A high-speed, high-resolution 3D printing process using powdered materials.
-
Subtractive Manufacturing (CNC Machining): This traditional method involves removing material from a block of raw material to create the desired shape. However, the integration of advanced digital control systems makes it a significant part of dimension technology. Computer Numerical Control (CNC) machines offer high precision and automation.
-
Hybrid Manufacturing: This increasingly common approach combines additive and subtractive techniques to leverage the strengths of both. For example, a 3D-printed part might undergo CNC machining for final finishing and precision.
Applications Across Industries:
The impact of dimension technology is far-reaching, with applications in diverse sectors:
- Aerospace: Creating lightweight, high-strength components with complex geometries.
- Automotive: Prototyping and producing customized parts, tooling, and jigs.
- Medical: Producing personalized implants, prosthetics, and surgical tools.
- Consumer Goods: Creating customized products, toys, and jewelry.
- Architecture: Building scale models and creating complex building components.
Advantages of Dimension Technology:
- Rapid Prototyping: Quickly create prototypes to test designs and functionality.
- Customization: Produce unique, tailored products for individual customers.
- Reduced Lead Times: Accelerate the manufacturing process and shorten delivery times.
- Lower Costs (in some cases): Reduce material waste and labor costs, especially for smaller production runs.
- Complex Designs: Create intricate designs that are impossible with traditional methods.
Limitations of Dimension Technology:
- Material Limitations: Not all materials can be used in all 3D printing processes.
- Scalability: Scaling up production can be challenging for some techniques.
- Post-Processing: Some 3D-printed parts require post-processing, such as sanding or painting.
- Cost of Equipment: The initial investment in 3D printers and other equipment can be significant.
- Accuracy and Tolerance: While improving rapidly, the accuracy of some 3D printing processes may not match traditional methods in all applications.
The Future of Dimension Technology:
The field of dimension technology is constantly evolving. Future advancements are likely to include:
- New Materials: Development of new materials with improved properties.
- Faster Printing Speeds: Increased efficiency and throughput.
- Improved Accuracy and Resolution: Creating even more detailed and precise parts.
- AI Integration: Utilizing artificial intelligence to optimize designs and processes.
- Increased Automation: Further automation of the entire manufacturing process.
Conclusion:
Dimension technology represents a significant leap forward in manufacturing and design. While it faces challenges, its potential to revolutionize industries is undeniable. As the technology continues to advance, we can expect to see even more innovative applications and a greater integration into our daily lives. Understanding its capabilities and limitations is crucial for businesses and individuals looking to leverage its transformative power.
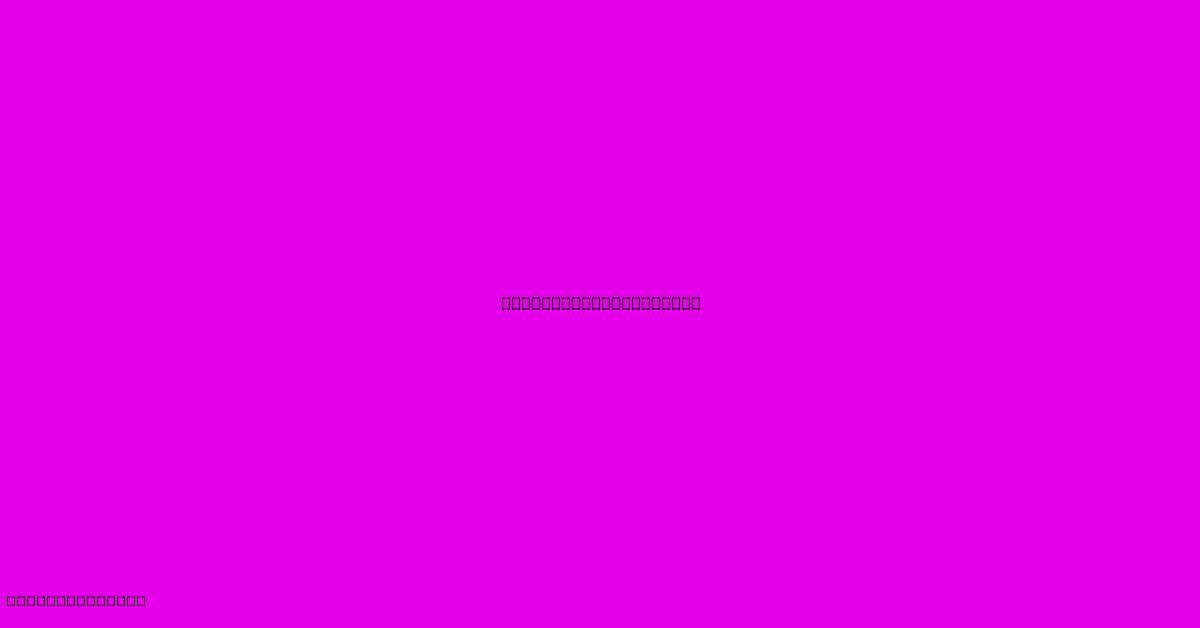
Thank you for visiting our website wich cover about Dimension Technology. We hope the information provided has been useful to you. Feel free to contact us if you have any questions or need further assistance. See you next time and dont miss to bookmark.
Featured Posts
-
Emory Information Technology
Dec 26, 2024
-
Key Technology Walla Walla
Dec 26, 2024
-
Konstas Debut Bumrahs Riposte
Dec 26, 2024
-
Assistive Technology For Mathematics
Dec 26, 2024
-
Durant Beal Power Suns Win Avenge Loss
Dec 26, 2024