Cutting Tool Technology
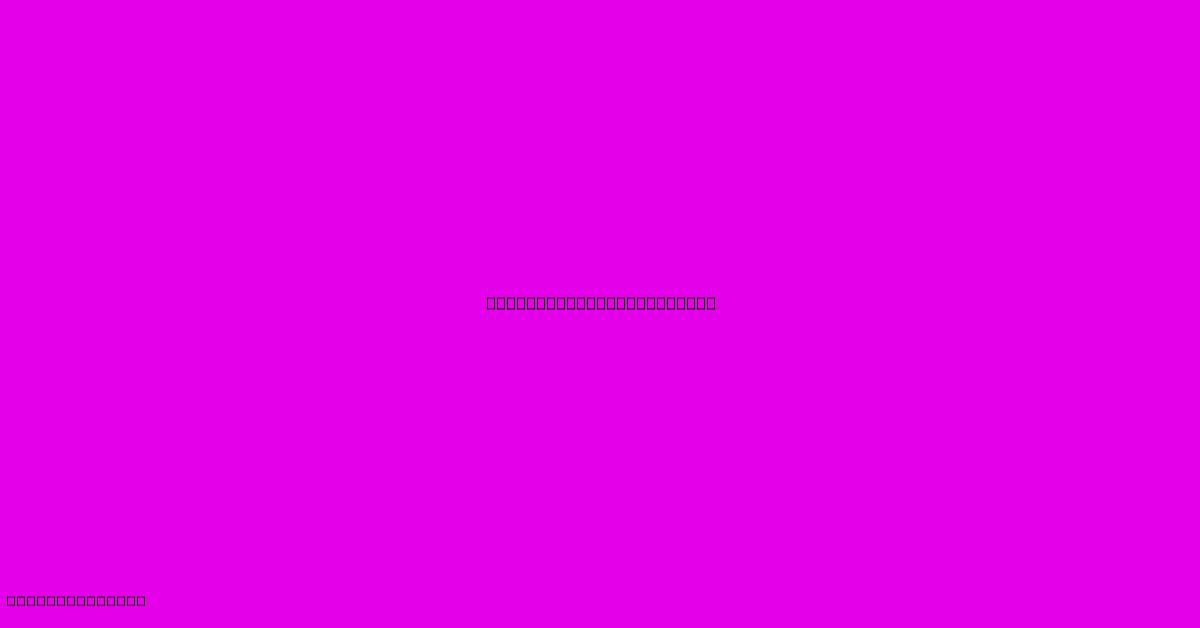
Discover more detailed and exciting information on our website. Click the link below to start your adventure: Visit Best Website mr.cleine.com. Don't miss out!
Table of Contents
Revolutionizing Machining: A Deep Dive into Cutting Tool Technology
Cutting tool technology is the backbone of numerous manufacturing processes, driving innovation across diverse industries. From aerospace to automotive, medical devices to consumer goods, the precision and efficiency of machining operations rely heavily on the advancements in cutting tool materials, geometries, and coatings. This article explores the evolution, current state, and future trends of this critical field.
The Evolution of Cutting Tools:
The history of cutting tools spans millennia, from rudimentary stone tools to the sophisticated carbide, ceramic, and diamond-based instruments used today. This evolution can be broadly categorized into several phases:
- Early Tools (Stone, Bronze, Iron): These tools were limited in hardness and durability, leading to low machining speeds and poor surface finishes.
- High-Speed Steel (HSS): The introduction of HSS in the late 19th century marked a significant leap, allowing for higher cutting speeds and improved tool life.
- Cemented Carbides: The development of cemented carbides in the early 20th century revolutionized machining. These materials offered significantly greater hardness and wear resistance than HSS, enabling even higher speeds and feeds.
- Ceramics and CBN/PCD: Ceramics, cubic boron nitride (CBN), and polycrystalline diamond (PCD) tools emerged later, pushing the boundaries of machining performance further. These materials are particularly suited for machining hard-to-machine materials like hardened steels, ceramics, and composites.
Current Cutting Tool Materials and their Applications:
Today's cutting tool market offers a wide array of materials, each with its own strengths and weaknesses:
- High-Speed Steel (HSS): Still widely used for general-purpose machining operations, particularly where cost is a primary factor.
- Cemented Carbides: Remain the workhorse of modern machining, offering excellent performance for a broad range of materials and applications. Different carbide grades are tailored for specific materials and machining conditions.
- Ceramics: Ideal for machining hard and brittle materials like cast iron, hardened steels, and ceramics, offering superior wear resistance.
- Cubic Boron Nitride (CBN): Exceptional for machining hardened steels, offering significantly longer tool life compared to carbides.
- Polycrystalline Diamond (PCD): The hardest cutting tool material available, ideal for machining non-ferrous materials like aluminum, graphite, and composites, boasting extremely long tool life.
The Role of Coatings:
Coatings play a crucial role in enhancing the performance of cutting tools. These thin layers, typically applied using techniques like Physical Vapor Deposition (PVD) or Chemical Vapor Deposition (CVD), provide several key benefits:
- Increased Wear Resistance: Coatings act as a barrier against wear and abrasion, extending tool life.
- Improved Heat Resistance: Coatings reduce the heat transfer from the cutting edge to the tool body, maintaining cutting edge integrity at higher speeds and feeds.
- Enhanced Lubrication: Certain coatings improve lubricity, reducing friction and heat generation.
- Improved Chip Control: Coatings can affect the chip formation process, leading to improved chip evacuation and surface finish.
Cutting Tool Geometries:
Cutting tool geometry is another critical factor impacting machining performance. The shape and angles of the cutting edge significantly influence factors like cutting forces, surface finish, and chip formation. Design considerations include:
- Rake Angle: Influences cutting forces and chip formation.
- Relief Angle: Affects tool strength and wear resistance.
- Cutting Edge Radius: Impacts surface finish and tool life.
Future Trends in Cutting Tool Technology:
The field of cutting tool technology is continuously evolving, with several key trends shaping the future:
- Advanced Materials: Research focuses on developing new materials with even greater hardness, wear resistance, and thermal stability.
- Smart Tools: Integration of sensors and data analytics to monitor tool condition, optimize machining parameters, and predict tool failure.
- Additive Manufacturing: 3D printing techniques are being explored for the creation of complex tool geometries and customized tooling solutions.
- Sustainable Manufacturing: Focus on developing environmentally friendly cutting tool materials and processes.
Conclusion:
Cutting tool technology is a dynamic field critical to modern manufacturing. The continuous advancements in materials, coatings, geometries, and manufacturing processes are driving improvements in machining efficiency, precision, and sustainability. As technology continues to evolve, we can expect even more significant advancements in cutting tool technology, paving the way for more efficient and productive machining processes across various industries.
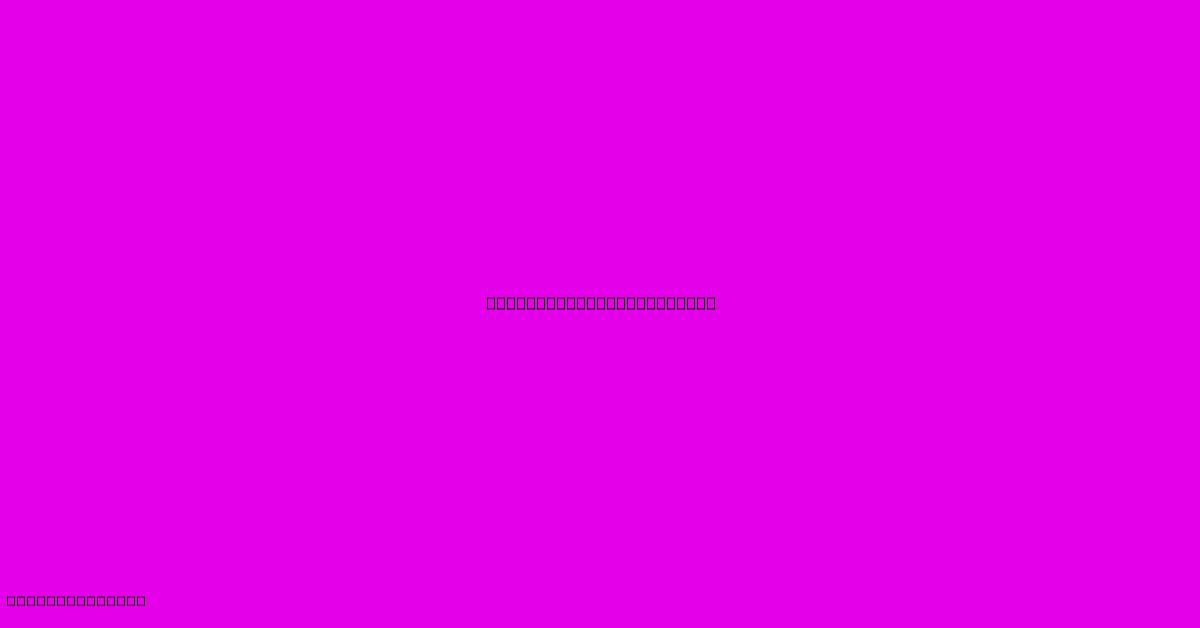
Thank you for visiting our website wich cover about Cutting Tool Technology. We hope the information provided has been useful to you. Feel free to contact us if you have any questions or need further assistance. See you next time and dont miss to bookmark.
Featured Posts
-
Cl Technologies
Dec 27, 2024
-
Jackson Nfl Verpasst Chance
Dec 27, 2024
-
Definitive Technology Soundbar
Dec 27, 2024
-
Berthold Technologies
Dec 27, 2024
-
Wolves Se Oorwinning Oor Man Utd
Dec 27, 2024