Custom Sensors & Technologies
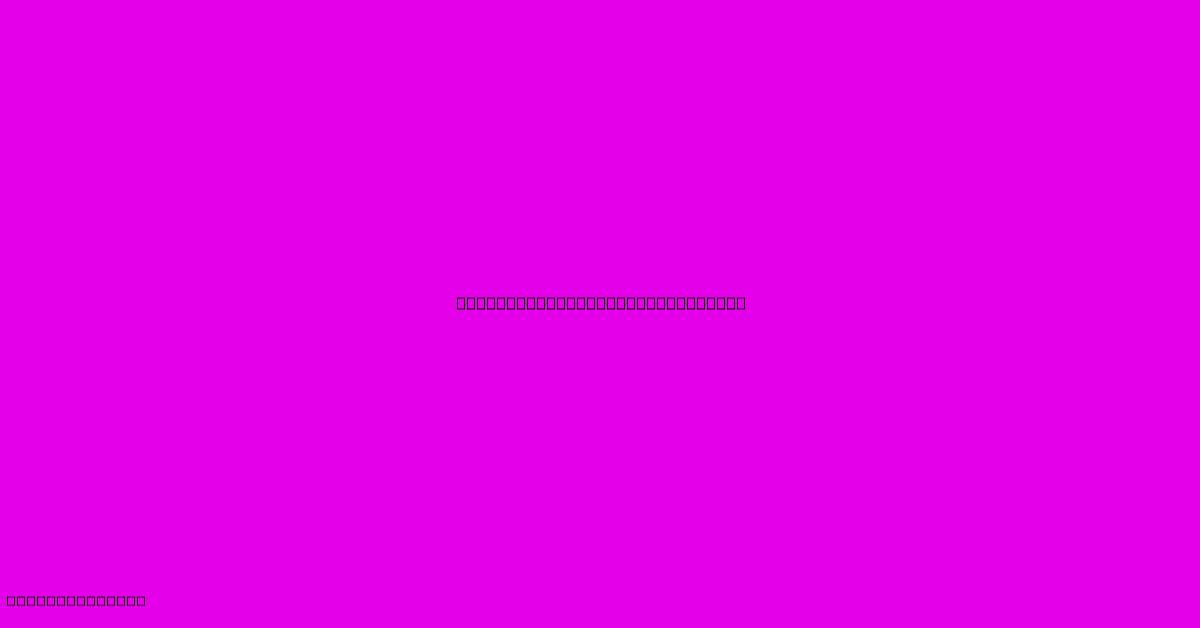
Discover more detailed and exciting information on our website. Click the link below to start your adventure: Visit Best Website mr.cleine.com. Don't miss out!
Table of Contents
Custom Sensors & Technologies: Tailoring Solutions for Unique Needs
The world of sensing is exploding. Off-the-shelf sensors offer a wealth of options, but for truly innovative applications and optimal performance, custom sensor and technology solutions are often necessary. This article delves into the world of custom sensors, exploring their benefits, design considerations, and the industries they transform.
Why Choose Custom Sensors?
Standard, commercially available sensors serve many purposes. However, situations arise where their limitations become apparent. This is where custom-designed sensors step in, offering unparalleled advantages:
-
Enhanced Performance: Custom sensors can be optimized for specific parameters like sensitivity, accuracy, range, and response time, exceeding the capabilities of general-purpose devices. Need a sensor with extreme precision in a narrow temperature range? A custom solution is the answer.
-
Unique Form Factors: Standard sensors often come in standardized packages. Custom designs allow for integration into challenging environments or spaces with limited accessibility. This is crucial for applications in robotics, medical devices, and aerospace.
-
Specific Materials and Processes: Custom sensors allow the use of materials and manufacturing processes best suited to the application's operating conditions. Extreme temperatures, corrosive chemicals, or high pressure environments demand tailored materials and construction.
-
Integration with Existing Systems: Seamless integration with complex systems is often a major challenge. Custom sensors can be designed to plug directly into existing infrastructure, reducing integration time and costs.
-
Cost-Effectiveness (Long-term): While initial investment might be higher, custom sensors can deliver significant long-term cost savings through improved efficiency, reduced downtime, and optimized performance, particularly in high-volume applications.
Designing a Custom Sensor: Key Considerations
Designing a custom sensor is a complex process involving several key steps:
-
Defining Requirements: Clearly outlining the sensor's purpose, operating environment, required accuracy, and other critical specifications is paramount. This forms the foundation of the design process.
-
Choosing the Right Technology: Selecting appropriate sensing technology (optical, capacitive, inductive, piezoelectric, etc.) is crucial. The choice depends on the target measurand (the physical quantity being measured) and the application's constraints.
-
Material Selection: Material choices influence sensor performance, durability, and cost. Considerations include biocompatibility (for medical applications), thermal stability, and resistance to corrosion.
-
Signal Processing and Conditioning: The sensor's raw signal often requires amplification, filtering, and other processing steps to ensure accuracy and compatibility with the target system.
-
Packaging and Integration: Careful consideration should be given to the sensor's packaging, ensuring protection from environmental factors and facilitating easy integration into the end application.
-
Testing and Calibration: Rigorous testing and calibration are essential to verify the sensor's accuracy and reliability under diverse operating conditions.
Industries Benefiting from Custom Sensor Technologies
Custom sensors and technologies are revolutionizing various industries:
-
Healthcare: Advanced medical devices, implantable sensors, and point-of-care diagnostics rely heavily on customized sensing solutions for precise and reliable measurements.
-
Automotive: Improved safety systems, advanced driver-assistance systems (ADAS), and autonomous vehicles require highly accurate and robust sensors for environmental perception.
-
Industrial Automation: Custom sensors are vital for process optimization, quality control, and predictive maintenance in manufacturing settings.
-
Aerospace: Reliable and accurate sensors are crucial for aircraft navigation, engine monitoring, and structural health monitoring.
-
Environmental Monitoring: Custom sensors play a key role in air and water quality monitoring, pollution detection, and climate research.
Conclusion
Custom sensors represent a powerful tool for addressing unique sensing challenges. By carefully considering the design parameters and selecting the appropriate technologies, manufacturers can create tailored solutions that improve performance, efficiency, and reliability across a range of industries. The future of sensing lies in the continued innovation and development of custom solutions to meet the ever-evolving demands of advanced applications.
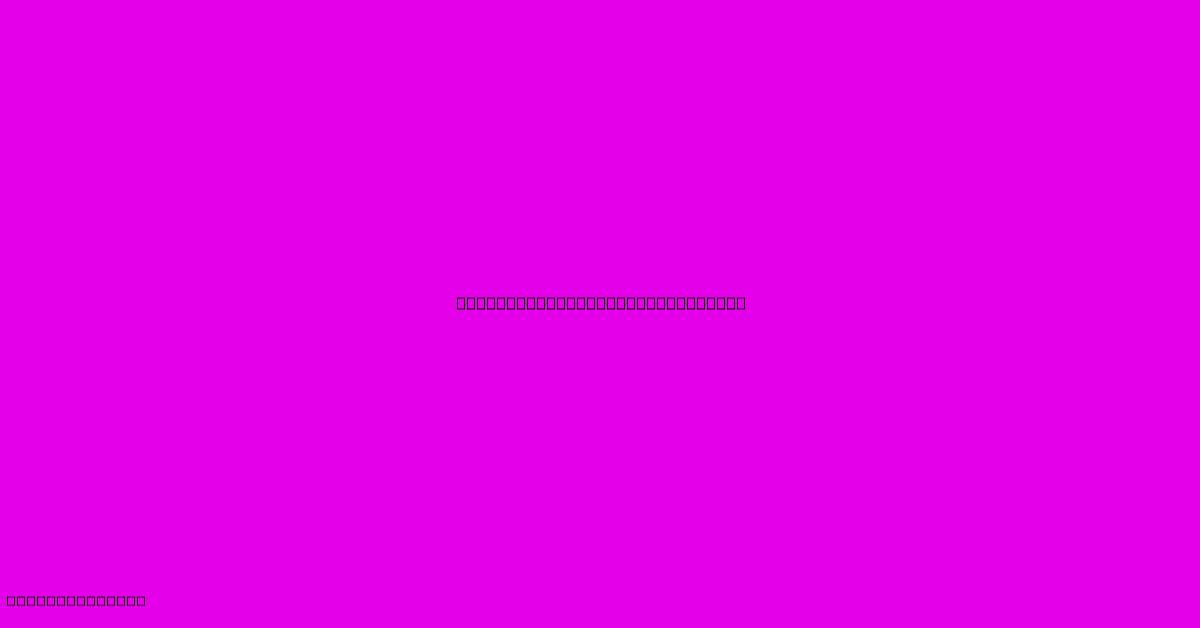
Thank you for visiting our website wich cover about Custom Sensors & Technologies. We hope the information provided has been useful to you. Feel free to contact us if you have any questions or need further assistance. See you next time and dont miss to bookmark.
Featured Posts
-
Instructional Technology Positions
Dec 25, 2024
-
Concerto Natale Il Volo Canali Tv
Dec 25, 2024
-
Holiday Mega Millions 1 15 Billion
Dec 25, 2024
-
Cloudreach Technology
Dec 25, 2024
-
How Do Nations Mostly Use Technology In Foreign Relations
Dec 25, 2024