Cold Spray Technology
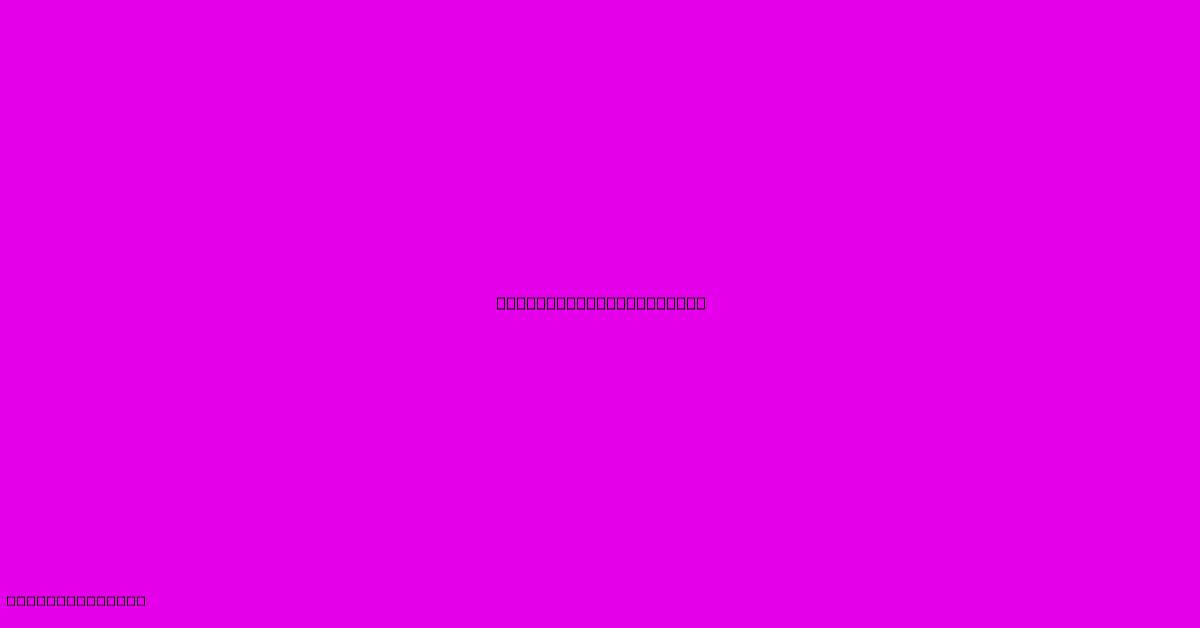
Discover more detailed and exciting information on our website. Click the link below to start your adventure: Visit Best Website mr.cleine.com. Don't miss out!
Table of Contents
Cold Spray Technology: A Revolutionary Coating Method
Cold spray technology is a groundbreaking additive manufacturing process used to deposit a wide range of materials onto various substrates. Unlike traditional thermal spray methods, which rely on high temperatures to melt and propel particles, cold spray utilizes high-velocity particles at relatively low temperatures. This key difference results in a number of significant advantages, making cold spray a rapidly growing technology across diverse industries.
The Science Behind Cold Spray:
The process involves accelerating fine powder particles to supersonic speeds (typically Mach 2-3) using compressed gas, usually air or nitrogen. These high-velocity particles then impact the substrate. The kinetic energy of the particles is sufficient to deform them plastically upon impact, creating a strong metallurgical bond with the substrate without melting. This bonding mechanism is crucial and distinguishes cold spray from other coating methods.
Key parameters influencing the success of cold spray include:
- Particle velocity: Must exceed a critical velocity for successful bonding.
- Particle size and morphology: Optimum particle size and shape are crucial for efficient deposition and coating quality.
- Gas pressure and temperature: Affect particle velocity and the overall process efficiency.
- Substrate material and surface preparation: Surface roughness and cleanliness influence bond strength.
Advantages of Cold Spray Technology:
The unique characteristics of cold spray offer several advantages over traditional coating methods:
- No melting: This prevents undesirable chemical reactions and phase transformations, preserving the material's properties in the coating. This is particularly advantageous for materials with low melting points or those prone to oxidation.
- High deposition efficiency: A significant portion of the sprayed particles bond with the substrate, minimizing material waste.
- Strong metallurgical bond: Results in exceptional adhesion and coating integrity, even on challenging substrates.
- Room temperature processing: Minimizes distortion and residual stresses in the substrate and coating.
- Versatile material compatibility: Can be used with a wide range of materials, including metals, ceramics, and polymers.
- Thick coatings: Capable of producing coatings with significant thickness without compromising quality.
- Environmental benefits: Reduced energy consumption compared to other thermal spray methods.
Applications of Cold Spray Technology:
Cold spray is rapidly finding applications in various sectors:
- Aerospace: Repair and refurbishment of aircraft components, deposition of thermal barrier coatings, and the creation of lightweight, high-strength components.
- Automotive: Production of wear-resistant coatings for engine parts and improving the performance of fuel injectors.
- Energy: Corrosion protection for pipelines and components in power generation plants.
- Biomedical: Development of biocompatible coatings for implants and medical devices.
- Defense: Creation of protective coatings for military equipment and enhancing the performance of weaponry.
- Oil & Gas: Protection against corrosion and erosion in harsh environments.
Challenges and Future Directions:
Despite its significant advantages, cold spray technology faces some challenges:
- Scaling up: Developing cost-effective and efficient large-scale applications remains a challenge.
- Porosity control: Achieving consistent and low porosity in thick coatings requires further optimization of process parameters.
- Material limitations: Not all materials are suitable for cold spray processing; further research is needed to expand the range of compatible materials.
The future of cold spray technology appears bright. Ongoing research focuses on improving process control, expanding material compatibility, and developing novel applications. As the technology matures and becomes more widely adopted, its impact on various industries is likely to grow significantly. It's a technology poised to revolutionize surface engineering and additive manufacturing.
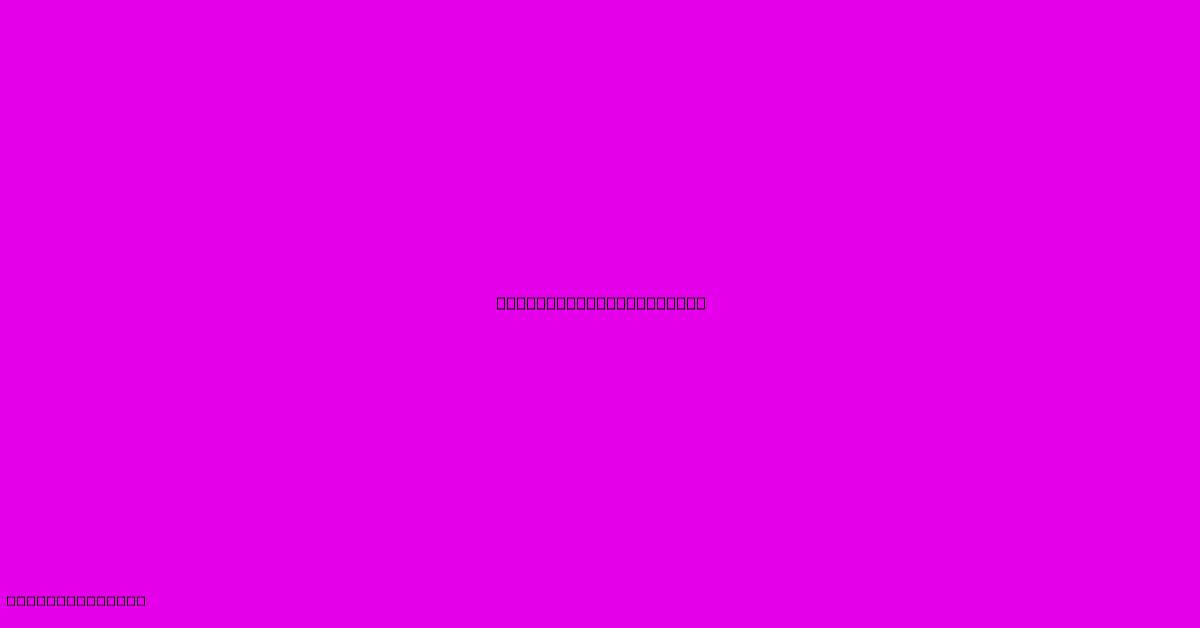
Thank you for visiting our website wich cover about Cold Spray Technology. We hope the information provided has been useful to you. Feel free to contact us if you have any questions or need further assistance. See you next time and dont miss to bookmark.
Featured Posts
-
Ibex Technologies
Dec 31, 2024
-
Jorge Lanata Muere El Periodista Argentino
Dec 31, 2024
-
Aecom Technology Corp
Dec 31, 2024
-
Google Doodle A A A A Y A A A Y A A A A A Ye A A A A A A A A Y A A A A A A A A Y A A A A A A Y A A A A Y A A A Y Google Doodle A A A A Y A A A Y A A A A Y A A A Y A A A A Y A A Ya Y A A A A Y A A A A A A Y A A A Y A A A A Y A A A Y A A A A Y A A Ya Y
Dec 31, 2024
-
Falcons Season In Jeopardy After Loss
Dec 31, 2024