Cold Forming Technology
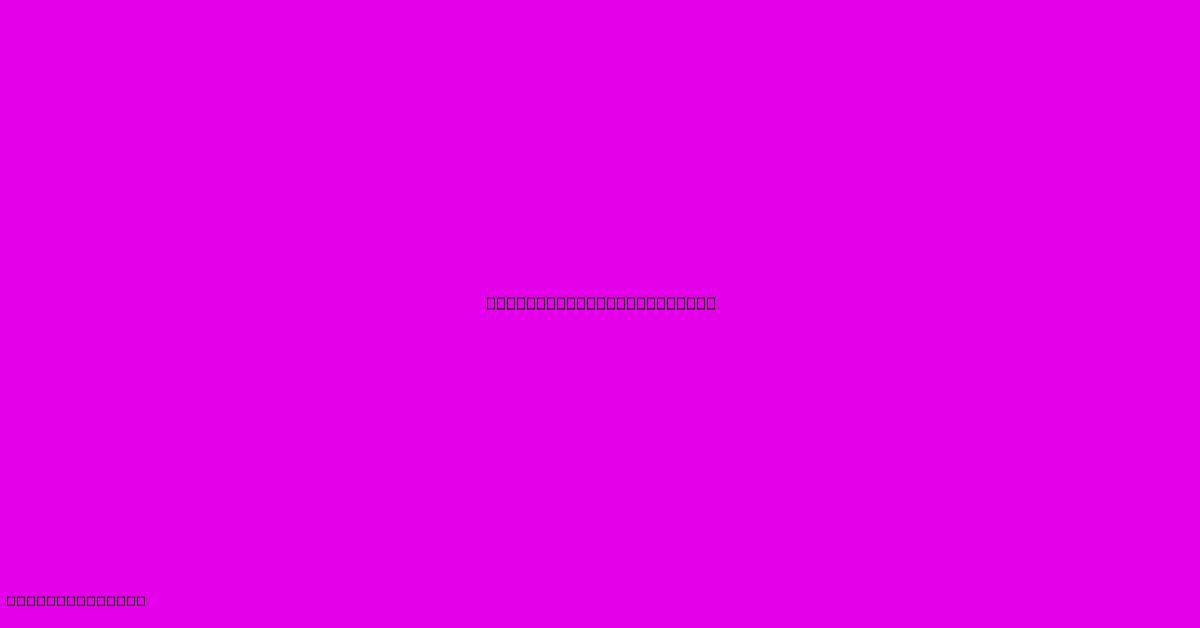
Discover more detailed and exciting information on our website. Click the link below to start your adventure: Visit Best Website mr.cleine.com. Don't miss out!
Table of Contents
Cold Forming Technology: Shaping the Future of Manufacturing
Cold forming, a versatile and efficient metalworking process, is rapidly transforming manufacturing industries. This article delves into the intricacies of cold forming technology, exploring its principles, advantages, applications, and future trends.
What is Cold Forming?
Cold forming, also known as cold forging, is a metal forming process where a metal workpiece is shaped at or near room temperature without the application of heat. Unlike hot forming, cold forming utilizes specialized tooling and significant pressure to deform the metal, achieving precise shapes and high dimensional accuracy. This process typically involves techniques such as stamping, pressing, coining, and extrusion.
The Principles Behind Cold Forming
The process relies on the metal's plasticity, its ability to deform permanently without fracturing. The applied force causes the metal's crystal structure to realign, resulting in the desired shape. This deformation leads to increased strength and hardness compared to the original material, a phenomenon known as work hardening or strain hardening.
Advantages of Cold Forming Technology:
Cold forming offers several significant advantages over hot forming:
- Improved Mechanical Properties: Work hardening increases the material's strength, hardness, and fatigue resistance. This results in parts that are more durable and longer-lasting.
- High Dimensional Accuracy: Cold forming allows for precise control over the dimensions and tolerances of the finished product, minimizing the need for secondary machining operations.
- Enhanced Surface Finish: The process generally produces parts with a superior surface finish compared to hot forming, often eliminating the need for additional surface treatments.
- Increased Production Efficiency: Cold forming is a relatively fast process, leading to higher production rates and lower manufacturing costs.
- Material Savings: Because of precise shaping, less material waste occurs compared to processes involving significant machining.
- Improved Product Consistency: Cold forming results in highly consistent parts with minimal variations in dimensions and properties.
Applications of Cold Forming:
Cold forming technology finds wide application across diverse industries:
- Automotive Industry: Production of various components including fasteners (nuts, bolts, screws), gears, shafts, and other complex parts.
- Aerospace Industry: Manufacturing of high-strength, lightweight components that require precise tolerances and exceptional durability.
- Electronics Industry: Creation of miniature components for electronic devices, such as connectors and contacts.
- Medical Industry: Production of implants, surgical instruments, and other medical devices.
- Construction Industry: Manufacturing of fasteners and structural components.
Types of Cold Forming Processes:
Several cold forming techniques exist, each suitable for different applications:
- Cold Heading: Forming the head of a fastener using a punch and die.
- Impact Extrusion: Forging a workpiece using a high-speed impact.
- Cold Roll Forming: Shaping metal into continuous lengths using a series of rollers.
- Coining: Producing highly accurate, intricate shapes using extremely high pressures.
- Progressive Die Stamping: Forming a part in several stages using a single die.
Future Trends in Cold Forming Technology:
The field is constantly evolving, with several key trends shaping its future:
- Advanced Materials: Increasing use of high-strength alloys and advanced materials to create even stronger and more lightweight components.
- Automation and Robotics: Greater automation and integration of robotics to increase production efficiency and consistency.
- Simulation and Modeling: Advanced simulation techniques to optimize the cold forming process and predict part performance.
- Hybrid Processes: Combining cold forming with other manufacturing processes such as additive manufacturing (3D printing) to create complex, high-performance components.
Conclusion:
Cold forming technology is a vital part of modern manufacturing, offering a compelling combination of precision, efficiency, and material optimization. As the technology continues to advance, its applications will expand further, playing a crucial role in shaping the products and industries of the future.
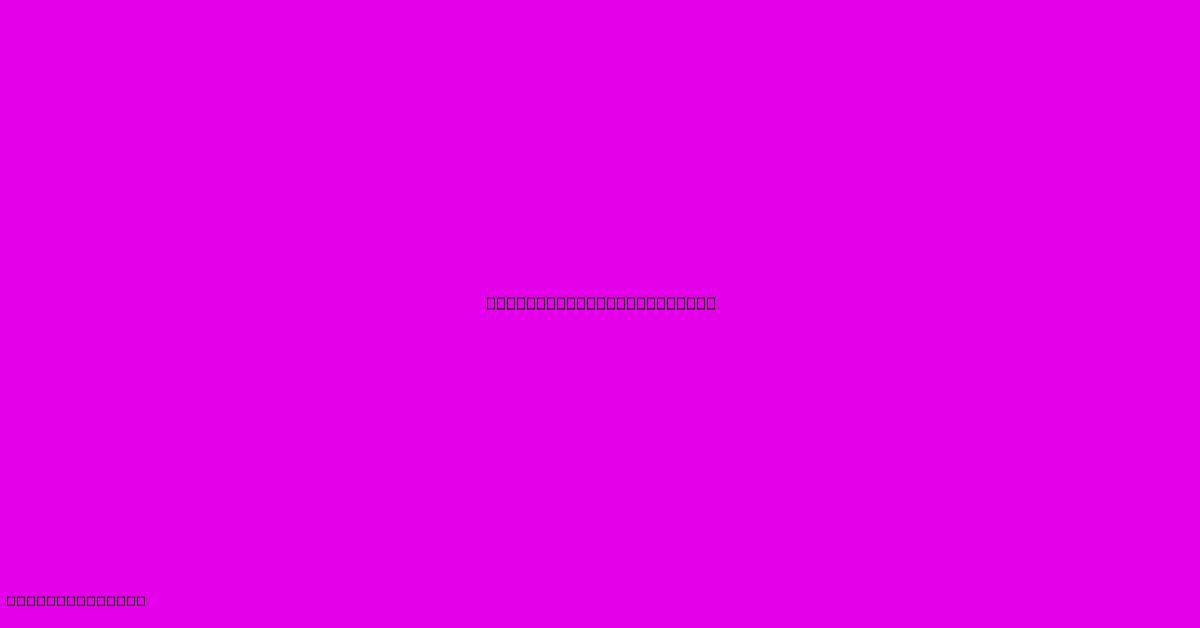
Thank you for visiting our website wich cover about Cold Forming Technology. We hope the information provided has been useful to you. Feel free to contact us if you have any questions or need further assistance. See you next time and dont miss to bookmark.
Featured Posts
-
Imiter Pere Noel Grand Concours Ho Ho Ho
Dec 25, 2024
-
Concerto Natale Il Volo Canali Tv
Dec 25, 2024
-
Technology And Crime
Dec 25, 2024
-
Beijing Balance Medical Technology
Dec 25, 2024
-
Master In Instructional Technology
Dec 25, 2024