Cnc Technology
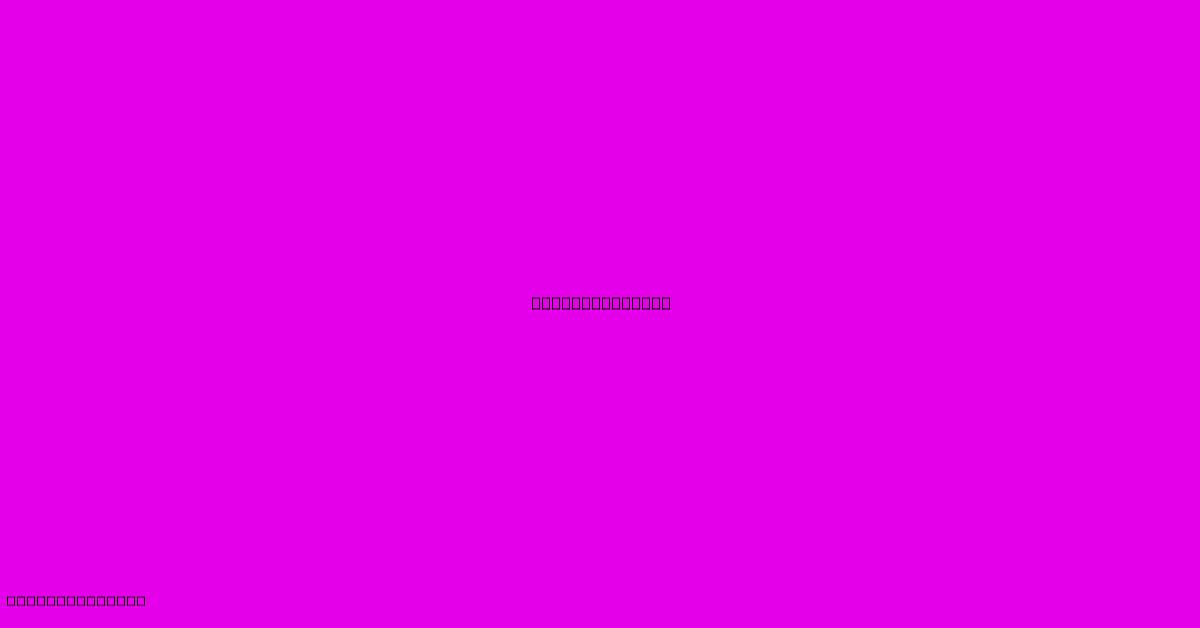
Discover more detailed and exciting information on our website. Click the link below to start your adventure: Visit Best Website mr.cleine.com. Don't miss out!
Table of Contents
CNC Technology: Revolutionizing Manufacturing Precision
CNC, or Computer Numerical Control, technology has fundamentally reshaped modern manufacturing. This sophisticated process uses computer-aided design (CAD) and computer-aided manufacturing (CAM) software to control machine tools, enabling the precise creation of complex parts with unparalleled accuracy and efficiency. This article delves into the core principles, advantages, and applications of CNC technology.
What is CNC Technology?
At its heart, CNC technology involves programming instructions into a computer that then directs the movement and operation of machine tools. These tools, which can include mills, lathes, routers, and 3D printers, precisely cut, shape, and finish materials like metal, wood, plastic, and composites. The instructions, typically written in G-code, define the precise path the tool must follow to create the desired component.
The process begins with a digital design of the part created using CAD software. This design is then translated into the G-code instructions by CAM software. This G-code is then uploaded to the CNC machine's control unit, which directs the machine's motors and actuators to execute the programmed movements with micron-level precision.
Advantages of CNC Technology
The advantages of CNC technology are numerous and contribute to its widespread adoption across diverse industries:
-
High Precision and Accuracy: CNC machines can consistently produce parts with extremely tight tolerances, far exceeding the capabilities of manual methods. This is crucial for industries demanding high precision, such as aerospace, medical devices, and automotive manufacturing.
-
Increased Efficiency and Productivity: Automation inherent in CNC machining significantly speeds up production processes compared to manual machining. This leads to increased output and reduced manufacturing time.
-
Improved Repeatability and Consistency: CNC machines replicate the same part repeatedly with identical accuracy, eliminating variations associated with human intervention. This guarantees consistent quality and reduces waste due to rejected parts.
-
Enhanced Flexibility and Versatility: CNC machines can be programmed to create a wide variety of parts, simply by changing the G-code instructions. This versatility allows for quick adaptation to new designs and production requirements.
-
Reduced Labor Costs: While requiring skilled programmers and operators, CNC technology reduces the need for large numbers of manual machinists, leading to lower labor costs in the long run.
-
Complex Part Creation: CNC machining can create intricate and complex shapes and geometries that are impossible or impractical to produce manually. This opens up possibilities for innovative designs and advanced functionalities.
Applications of CNC Technology
The applications of CNC technology span a wide range of industries:
-
Aerospace: Manufacturing aircraft components, engines, and other precision parts demanding high accuracy and strength.
-
Automotive: Producing engine blocks, car bodies, and other critical components requiring precise tolerances and high volume production.
-
Medical Devices: Creating implants, prosthetics, and surgical tools requiring exceptional precision and biocompatibility.
-
Manufacturing: Producing a wide range of parts for various industries, from electronics and consumer goods to industrial equipment.
-
Tooling and Mold Making: Creating precise molds and dies used in injection molding, casting, and other manufacturing processes.
-
Art and Sculpture: Creating intricate designs and 3D sculptures, pushing the creative boundaries of traditional art forms.
The Future of CNC Technology
CNC technology continues to evolve, with advancements focusing on:
-
Additive Manufacturing (3D Printing): Integrating CNC capabilities with 3D printing technologies allows for even more complex designs and customized production.
-
Artificial Intelligence (AI): AI-powered CNC systems are enhancing optimization, predictive maintenance, and autonomous operations.
-
Internet of Things (IoT): Connected CNC machines provide real-time data analysis and remote monitoring, leading to improved efficiency and proactive maintenance.
In conclusion, CNC technology is a cornerstone of modern manufacturing, offering unparalleled precision, efficiency, and flexibility. Its continued development and integration with cutting-edge technologies promise even greater advancements in the future, shaping manufacturing processes across a wide range of industries.
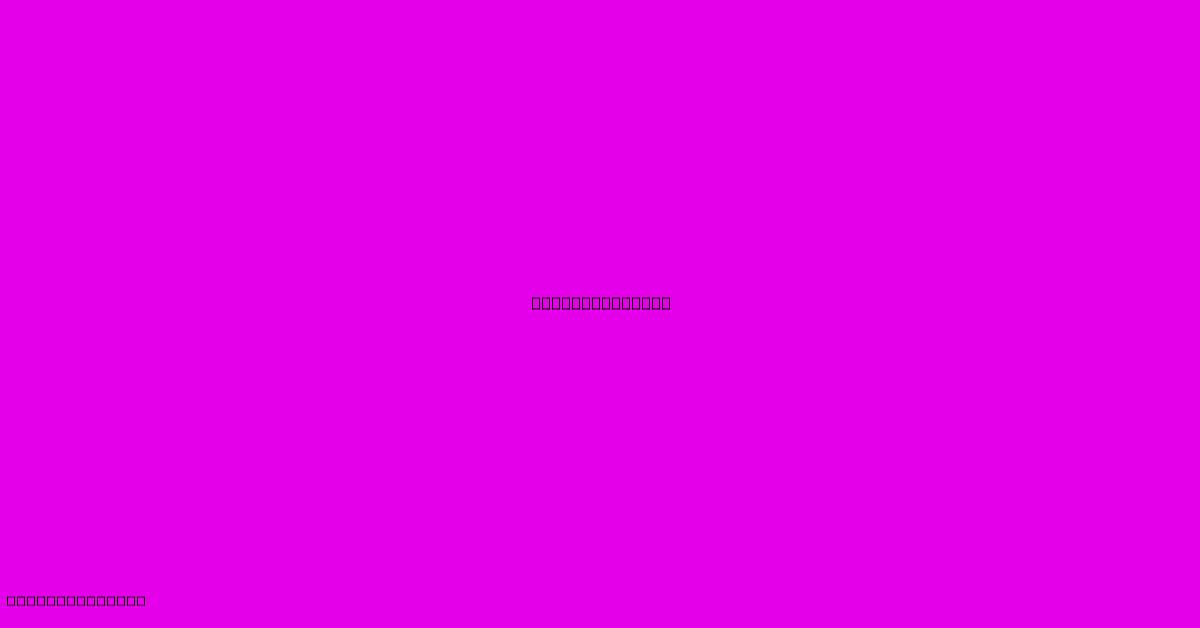
Thank you for visiting our website wich cover about Cnc Technology. We hope the information provided has been useful to you. Feel free to contact us if you have any questions or need further assistance. See you next time and dont miss to bookmark.
Featured Posts
-
Ukef Boosts Uk Exports Economy
Jan 01, 2025
-
Ddc Technologies Inc
Jan 01, 2025
-
Alabama Vs Michigan 2024 Bowl Prediction
Jan 01, 2025
-
Balenciaga Technology
Jan 01, 2025
-
Miles Technologies Reviews
Jan 01, 2025