Cmp Technology
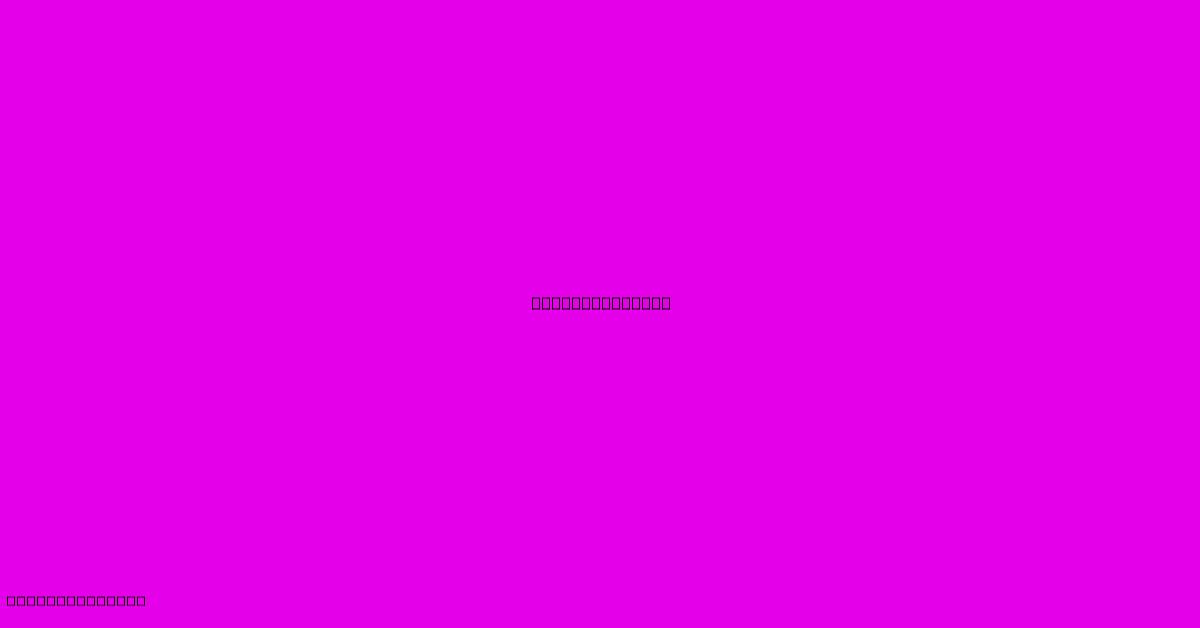
Discover more detailed and exciting information on our website. Click the link below to start your adventure: Visit Best Website mr.cleine.com. Don't miss out!
Table of Contents
CMP Technology: A Deep Dive into Chemical Mechanical Planarization
Chemical Mechanical Planarization (CMP) is a crucial process in semiconductor manufacturing, responsible for creating incredibly flat surfaces on silicon wafers. This process is essential for the creation of high-performance integrated circuits (ICs), impacting everything from smartphones to supercomputers. This article delves into the intricacies of CMP technology, exploring its principles, applications, and future trends.
Understanding the Fundamentals of CMP
CMP is a hybrid process combining chemical etching and mechanical polishing. A wafer is pressed against a rotating polishing pad, while a slurry—a mixture of abrasive particles and chemical etchants—is dispensed between the two. This synergistic action achieves planarization:
- Chemical Etching: The chemical components in the slurry selectively etch the wafer material, removing high points more aggressively. This ensures a more uniform removal rate.
- Mechanical Polishing: The abrasive particles in the slurry, along with the pressure and friction from the rotating pad, physically remove material from the wafer surface. This helps to smooth out the surface and achieve a high degree of planarity.
The precise balance between chemical and mechanical action is crucial for effective CMP. The process parameters, such as pressure, speed, slurry composition, and pad type, are meticulously controlled to achieve the desired surface flatness and material removal rate.
Key Applications of CMP Technology
CMP's planarization capabilities are vital in multiple stages of semiconductor fabrication:
- Global Planarization: This is perhaps the most common application, ensuring a smooth surface for subsequent lithographic steps. Uneven surfaces can lead to defects and inconsistencies in the patterning process.
- Inter-level Dielectric (ILD) CMP: Removes excess dielectric material between layers of transistors, creating a flat surface for subsequent metallization.
- Metal CMP: Planarizes metal layers, ensuring proper contact between adjacent layers and reducing electrical resistance.
- Shallow Trench Isolation (STI) CMP: Creates highly-precise, planarized isolation structures between transistors, enhancing performance and density.
The precision and control offered by CMP are critical for achieving the ever-increasing density and performance of modern integrated circuits. Without CMP, the fabrication of advanced chips would be practically impossible.
Advantages and Challenges of CMP
Advantages:
- High Planarity: Achieves extremely flat surfaces, essential for advanced lithography and subsequent processing steps.
- High Throughput: CMP processes can handle multiple wafers simultaneously, ensuring high production efficiency.
- Versatility: Applicable to a wide range of materials used in semiconductor manufacturing.
Challenges:
- Process Complexity: Optimizing CMP parameters requires significant expertise and precise control. Variations in wafer properties can significantly impact the results.
- Slurry Waste Management: CMP slurries can contain hazardous materials, necessitating careful waste management and environmental considerations.
- Defect Generation: While CMP planarizes the surface, it can also introduce defects, such as scratches or pits, which negatively affect device performance. Minimizing defect generation is a continuous area of research.
- Cost: CMP equipment and consumables are expensive, representing a significant investment for semiconductor manufacturers.
Future Trends in CMP Technology
Ongoing research and development focus on improving CMP performance and addressing its challenges:
- Advanced Slurry Development: Formulations are being developed to improve selectivity, reduce defects, and enhance environmental friendliness.
- Intelligent Process Control: Advanced sensors and machine learning algorithms are being integrated to optimize process parameters in real-time.
- New Pad Technologies: Improved polishing pads are being developed to enhance material removal and reduce defects.
- Alternative Planarization Techniques: Researchers are exploring alternative techniques to complement or replace CMP in specific applications, although CMP remains the dominant planarization method.
Conclusion:
CMP technology is a cornerstone of modern semiconductor manufacturing, enabling the creation of increasingly complex and powerful integrated circuits. While challenges remain, ongoing innovation in slurry chemistry, process control, and equipment design will ensure that CMP continues to play a crucial role in the future of semiconductor technology. The relentless pursuit of improved performance, cost-effectiveness, and sustainability will drive further advancements in this critical area of microfabrication.
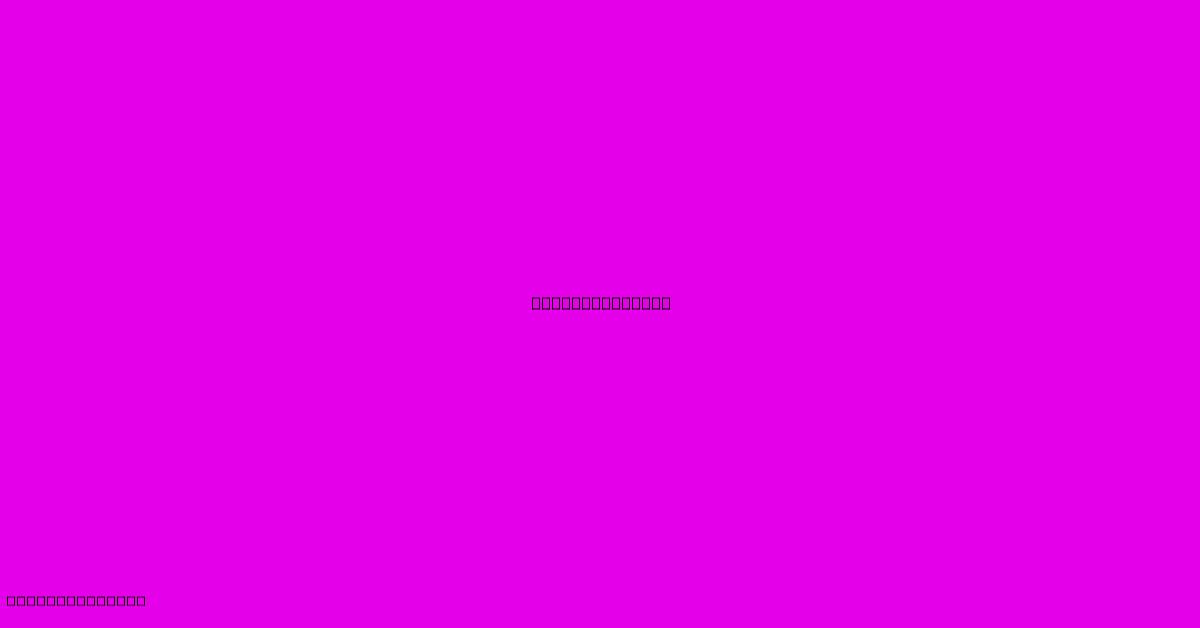
Thank you for visiting our website wich cover about Cmp Technology. We hope the information provided has been useful to you. Feel free to contact us if you have any questions or need further assistance. See you next time and dont miss to bookmark.
Featured Posts
-
Dulce Como Murio La Cantante
Dec 26, 2024
-
Americas Response Beyonce Concert
Dec 26, 2024
-
Chiefs Win Clinch Afc Top Seed
Dec 26, 2024
-
Mariah Carey Starts Netflix Nfl Christmas
Dec 26, 2024
-
Who Voices Wallace In 2024
Dec 26, 2024