Casting Technologies
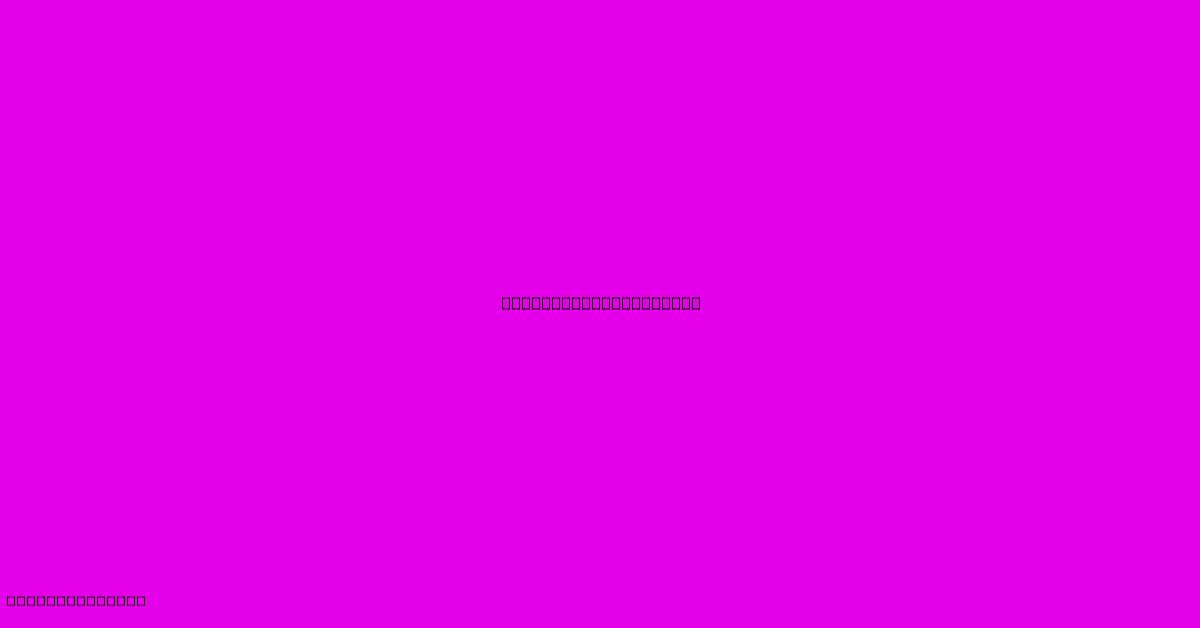
Discover more detailed and exciting information on our website. Click the link below to start your adventure: Visit Best Website mr.cleine.com. Don't miss out!
Table of Contents
Casting Technologies: Shaping the Future of Manufacturing
Casting is an ancient manufacturing process, but its modern iterations are anything but antiquated. From the intricate components of a jet engine to the everyday objects we use, casting technologies play a vital role in shaping our world. This article delves into the diverse world of casting, exploring its various methods, advantages, and applications.
What is Casting?
Casting involves pouring molten material into a mold, allowing it to solidify, and then removing the solidified part from the mold. This seemingly simple process yields incredibly complex shapes and offers a cost-effective method for mass production of many components. The choice of casting method depends on factors like the material, desired precision, and production volume.
Types of Casting Technologies
Several casting technologies exist, each with its strengths and limitations:
1. Sand Casting: This is the oldest and most widely used method. Molten metal is poured into a mold made of sand, typically a mixture of silica sand and binders. Sand casting is versatile and cost-effective for producing large parts, but dimensional accuracy is relatively low.
2. Investment Casting (Lost-Wax Casting): This precision casting technique uses a wax pattern that's coated in refractory material, creating an investment mold. The wax is melted out, and molten metal is poured into the mold. Investment casting produces highly accurate parts with complex geometries, often used in aerospace and medical applications.
3. Die Casting: This high-speed process uses metal molds (dies) to produce high-volume, high-precision parts. Molten metal is injected under high pressure into the die, resulting in intricate details and tight tolerances. Die casting is commonly used for automotive parts, electronics housings, and consumer goods.
4. Centrifugal Casting: Molten metal is poured into a spinning mold. Centrifugal force distributes the metal evenly, creating dense and uniform castings. This method is particularly useful for producing tubular parts like pipes and cylinders.
5. Continuous Casting: This method continuously produces long lengths of metal sections, such as slabs, billets, or blooms, by pouring molten metal into a mold that moves continuously. It's highly efficient for mass production of semi-finished metal products.
6. Shell Mold Casting: A metal pattern is coated with a mixture of sand and resin. This mixture hardens to form a shell mold, which is then used for casting. Shell mold casting offers a good balance between speed, accuracy, and cost-effectiveness.
Advantages of Casting
- Complex Shapes: Casting enables the creation of intricate and complex geometries that are difficult or impossible to achieve using other manufacturing processes.
- Cost-Effectiveness: Especially for high-volume production, casting offers a cost-effective method compared to machining or forging.
- Material Versatility: A wide range of metals and alloys can be cast, including steel, aluminum, iron, brass, and bronze.
- Large Part Sizes: Casting can produce components of significant size, which is limited by other methods.
Disadvantages of Casting
- Surface Finish: Castings may require further machining or finishing to achieve the desired surface quality.
- Dimensional Accuracy: Depending on the casting method, dimensional accuracy can vary.
- Porosity: Some castings may exhibit porosity, which can affect their strength and integrity.
- Waste Generation: The molding process can generate waste materials.
Applications of Casting Technologies
Casting technologies find applications across numerous industries:
- Automotive: Engine blocks, cylinder heads, transmission housings, wheels
- Aerospace: Turbine blades, aircraft components, engine parts
- Medical: Implants, surgical instruments, prosthetics
- Electronics: Computer housings, circuit boards, connectors
- Construction: Pipes, fittings, valves
- Consumer Goods: Kitchenware, toys, decorative items
The Future of Casting Technologies
Advancements in materials science, automation, and 3D printing are transforming the casting industry. Additive manufacturing techniques, for instance, are opening new possibilities for creating highly customized and complex parts. The future of casting lies in enhancing efficiency, precision, and sustainability, making it an even more indispensable manufacturing process.
By understanding the different types of casting technologies and their respective applications, manufacturers can select the optimal method to achieve their desired results. The continued innovation in this field will undoubtedly lead to further advancements and expansion of its capabilities.
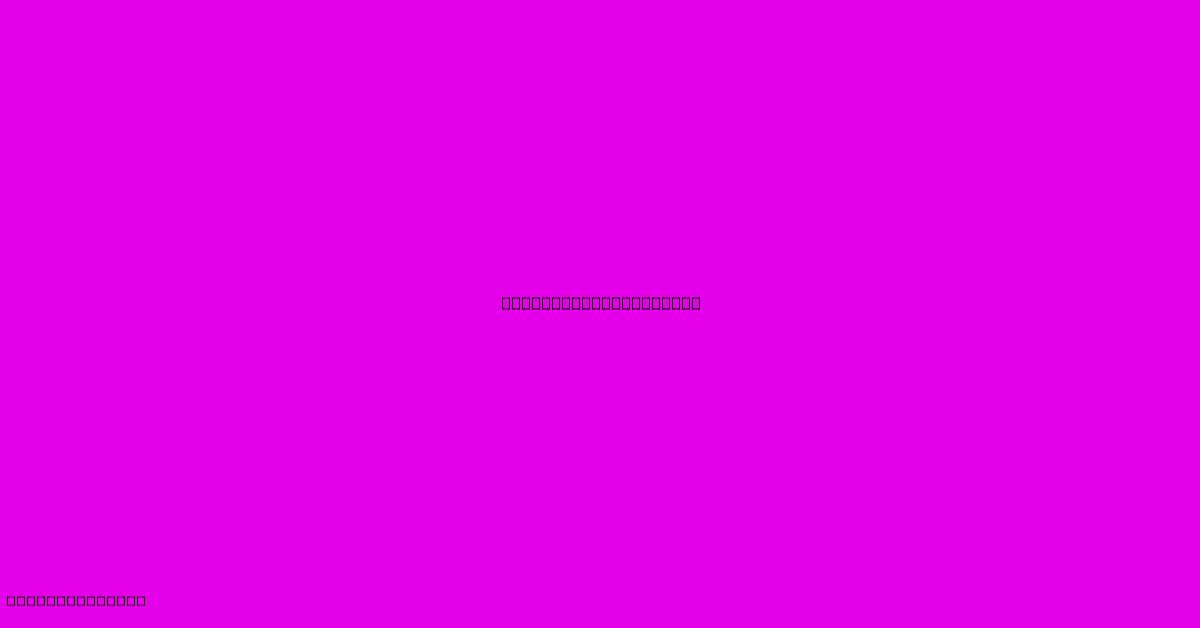
Thank you for visiting our website wich cover about Casting Technologies. We hope the information provided has been useful to you. Feel free to contact us if you have any questions or need further assistance. See you next time and dont miss to bookmark.
Featured Posts
-
Ablaze Technologies
Dec 25, 2024
-
Pirates Se 8 0 Oorwinning
Dec 25, 2024
-
Rozhdestvo V S Sh A Glavnye Zhelaniya Amerikantsev V 2024 Godu 56 Simvolov Utochnyaet Vremennoy Period Delaya Zagolovok Bolee Aktualnym
Dec 25, 2024
-
Hispanic Technology Inventors
Dec 25, 2024
-
Evacuation Tour Eiffel Incident Ascenseur
Dec 25, 2024