Bga Technology
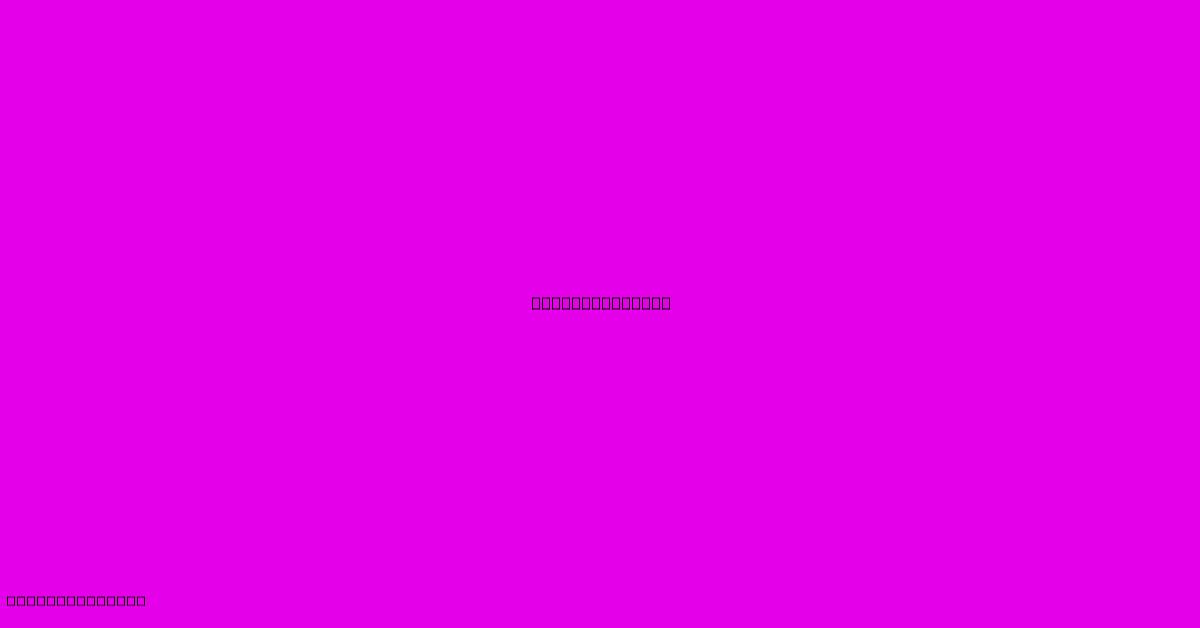
Discover more detailed and exciting information on our website. Click the link below to start your adventure: Visit Best Website mr.cleine.com. Don't miss out!
Table of Contents
BGA Technology: A Deep Dive into Ball Grid Array
Ball Grid Array (BGA) technology is a crucial component in modern electronics, enabling miniaturization and increased performance in various devices. Understanding BGA's intricacies is vital for anyone involved in electronics design, manufacturing, or repair. This article provides a comprehensive overview of BGA technology, exploring its advantages, disadvantages, and applications.
What is BGA Technology?
BGA is a surface-mount technology (SMT) where the integrated circuit (IC) is connected to the printed circuit board (PCB) via solder balls arranged in a grid pattern on the bottom of the chip. This arrangement contrasts with traditional through-hole and lead-frame packages, offering several significant advantages. Instead of leads extending from the sides of the chip, these solder balls provide the electrical connection, allowing for a denser and smaller package size.
Advantages of BGA Technology
- High Density: BGA's grid pattern allows for a significantly higher pin count in a smaller footprint than traditional packages like DIP or SOIC. This is crucial for high-performance devices requiring numerous connections.
- Improved Thermal Performance: The large surface area of the solder balls facilitates efficient heat dissipation, minimizing the risk of overheating and improving the reliability of the device.
- Miniaturization: BGA's compact design contributes to smaller and more portable electronic devices. This is particularly important for mobile phones, laptops, and other consumer electronics.
- Improved Signal Integrity: The shorter signal paths provided by BGA reduce signal attenuation and crosstalk, improving signal quality and performance.
- Cost-Effective (in mass production): While initial setup costs might be higher, BGA's automated assembly process leads to significant cost savings in large-scale manufacturing.
Disadvantages of BGA Technology
- Complex Assembly and Repair: BGA soldering requires specialized equipment and expertise, making assembly and repair more challenging compared to through-hole components. Microsoldering and specialized rework stations are often needed.
- Inspection Challenges: Inspecting the solder joints of a BGA package is more difficult due to the underside placement of the solder balls. X-ray inspection is frequently necessary.
- Higher Initial Costs: The specialized equipment and expertise needed for BGA manufacturing contribute to higher initial costs.
- Sensitivity to Damage: The small solder balls are susceptible to damage during handling and transportation. Careful handling is essential throughout the entire process.
Types of BGA Packages
Several variations of BGA packages exist, each with its own characteristics and applications:
- Plastic Ball Grid Array (PBGA): The most common type, using plastic packaging material.
- Ceramic Ball Grid Array (CBGA): Uses ceramic packaging, offering enhanced thermal performance and reliability.
- Land Grid Array (LGA): Similar to BGA but uses pads instead of solder balls. These are often used for processors and memory chips.
- Fine Pitch BGA (FPCBGA): Features significantly smaller ball pitches, further increasing density.
Applications of BGA Technology
BGA technology finds widespread application in a variety of electronic devices, including:
- Motherboards: Used for connecting CPUs, GPUs, and other critical components.
- Graphics Cards: Essential for connecting GPUs to the motherboard.
- Smartphones: Enables the integration of numerous high-performance components in a compact space.
- Laptops: Similar to smartphones, facilitating miniaturization and performance.
- Network Equipment: Used in routers, switches, and other networking hardware.
- Automotive Electronics: Increasingly used in advanced driver-assistance systems (ADAS) and other automotive applications.
Future Trends in BGA Technology
Continued miniaturization, higher pin counts, and improved thermal management remain key drivers for the evolution of BGA technology. Advancements in materials science and manufacturing processes are expected to further enhance the capabilities of BGA packages. The adoption of advanced packaging techniques, such as 3D stacking, is also poised to play a crucial role in the future of BGA.
Conclusion
Ball Grid Array technology is a cornerstone of modern electronics, enabling significant advancements in miniaturization, performance, and functionality. While challenges exist in assembly and repair, the advantages of BGA far outweigh the drawbacks, ensuring its continued dominance in a wide range of applications for years to come. Its evolution will continue to be shaped by the demands for increasingly powerful and compact electronic devices.
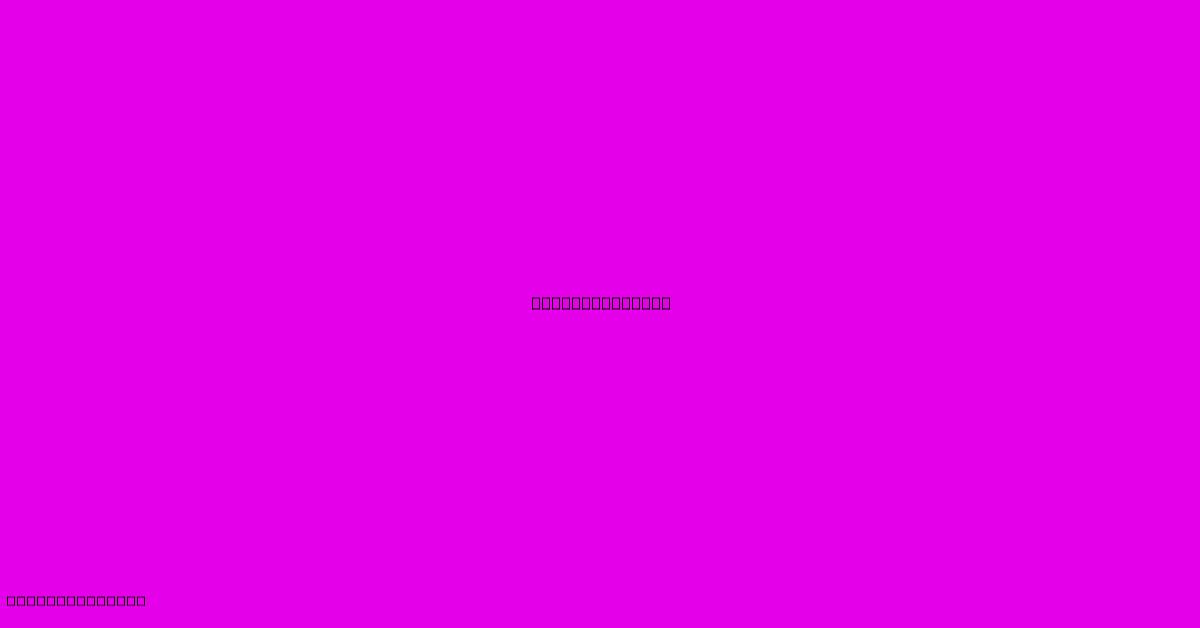
Thank you for visiting our website wich cover about Bga Technology. We hope the information provided has been useful to you. Feel free to contact us if you have any questions or need further assistance. See you next time and dont miss to bookmark.
Featured Posts
-
Label Technology
Dec 31, 2024
-
Broadway Tv Actress Linda Lavin Dies
Dec 31, 2024
-
Man Utd Vs Newcastle Final Score And Stats
Dec 31, 2024
-
Huawei Digital Power Technologies Co Ltd
Dec 31, 2024
-
Academy Of Information Technology
Dec 31, 2024