Advanced Corrosion Technologies And Training
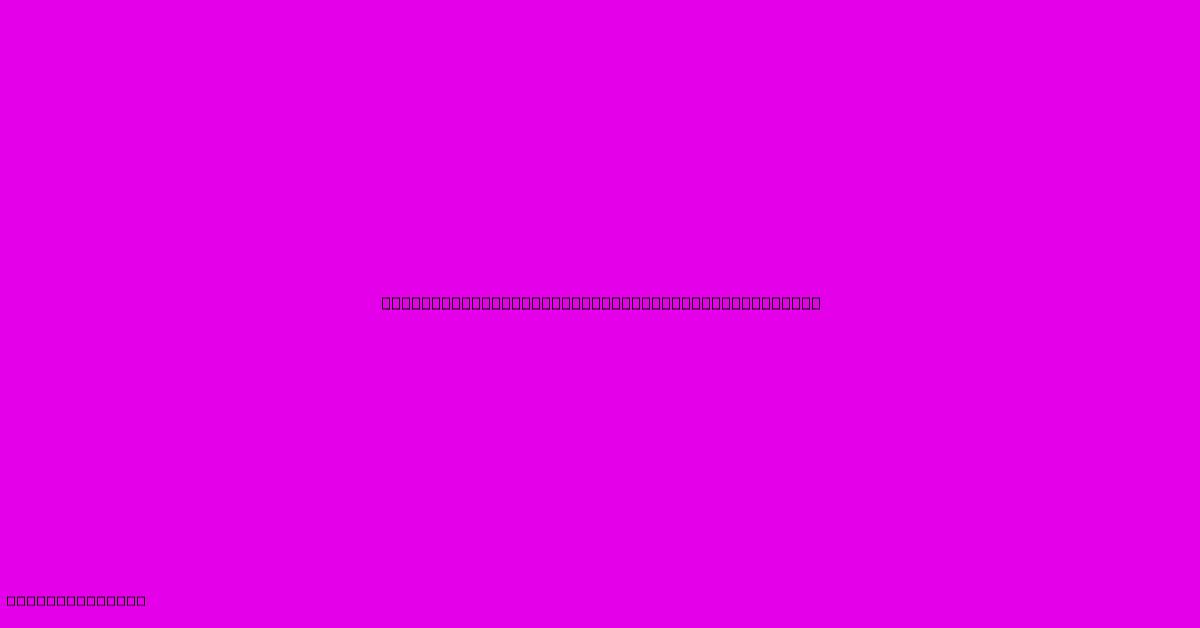
Discover more detailed and exciting information on our website. Click the link below to start your adventure: Visit Best Website mr.cleine.com. Don't miss out!
Table of Contents
Advanced Corrosion Technologies and Training: Protecting Your Assets from Degradation
Corrosion, the gradual deterioration of materials due to chemical or electrochemical reactions, presents a significant challenge across numerous industries. From infrastructure to manufacturing, the cost of corrosion damage is staggering, impacting safety, efficiency, and profitability. This article explores advanced corrosion technologies and the crucial role of specialized training in mitigating these risks.
Understanding the Spectrum of Corrosion Challenges:
Corrosion isn't a monolithic problem. It manifests in various forms, each requiring a tailored approach:
- Uniform Corrosion: A relatively predictable, even degradation across a surface.
- Pitting Corrosion: Localized, aggressive attack leading to deep pits.
- Crevice Corrosion: Corrosion concentrated in confined spaces, like gaps or joints.
- Stress Corrosion Cracking (SCC): A combination of tensile stress and corrosive environment causing cracking.
- Erosion Corrosion: Accelerated corrosion due to the combined action of a corrosive environment and fluid flow.
- Galvanic Corrosion: Electrochemical corrosion occurring when dissimilar metals are in contact.
Advanced Technologies for Corrosion Mitigation:
Addressing these varied challenges requires advanced technologies beyond traditional methods like coatings and inhibitors. Here are some key advancements:
1. Protective Coatings: The evolution of coatings extends beyond simple paints. We now see advanced materials like:
- High-performance polymers: Offering superior barrier properties and resistance to harsh environments.
- Ceramic coatings: Providing excellent thermal and chemical resistance.
- Metallic coatings: Offering enhanced corrosion protection through galvanization, metallization, or cladding.
2. Cathodic Protection: This electrochemical technique prevents corrosion by making the metal structure the cathode in an electrochemical cell. Advancements include:
- Impressed Current Cathodic Protection (ICCP): Uses an external power source to drive the protective current. Sophisticated monitoring systems optimize efficiency and prevent overprotection.
- Sacrificial Anodes: Utilizes more active metals that corrode preferentially, protecting the main structure. New anode materials offer extended lifespan and improved performance.
3. Corrosion Inhibitors: These chemicals slow down or prevent corrosion reactions. Advanced inhibitors are:
- Environmentally friendly: Reducing the ecological impact of corrosion control.
- Targeted: Designed to address specific corrosion mechanisms and environments.
- Smart inhibitors: Responding to changes in the environment to optimize protection.
4. Materials Selection and Design: Choosing corrosion-resistant materials is paramount. This includes:
- High-strength low-alloy steels: Offering improved strength and corrosion resistance.
- Stainless steels: Known for their excellent corrosion resistance in various environments.
- Nickel-based alloys: Providing exceptional resistance to highly corrosive conditions.
- Optimized designs: Minimizing crevices, stagnant areas, and other corrosion-prone features.
5. Non-destructive Testing (NDT): Regular inspection is crucial. Advanced NDT techniques include:
- Ultrasonic testing: Detects subsurface defects and corrosion.
- Eddy current testing: Measures changes in conductivity to detect corrosion.
- Radiographic testing: Uses X-rays or gamma rays to identify internal corrosion.
The Importance of Training:
Implementing these advanced technologies requires skilled professionals. Comprehensive training programs are essential, covering:
- Fundamentals of corrosion: Understanding the mechanisms and factors influencing corrosion.
- Advanced corrosion technologies: Detailed knowledge of the various mitigation techniques.
- Materials selection: Choosing the right materials for specific applications.
- NDT techniques: Performing effective inspections and identifying corrosion damage.
- Risk assessment and management: Developing strategies to minimize corrosion risks.
Conclusion:
Advanced corrosion technologies are continuously evolving, offering more effective and sustainable solutions. However, the successful application of these technologies hinges on properly trained personnel who can design, implement, and monitor corrosion control strategies. Investing in comprehensive training programs is crucial for protecting assets, ensuring safety, and maximizing operational efficiency. The cost of corrosion damage far outweighs the cost of effective prevention and management through training and the deployment of advanced technologies.
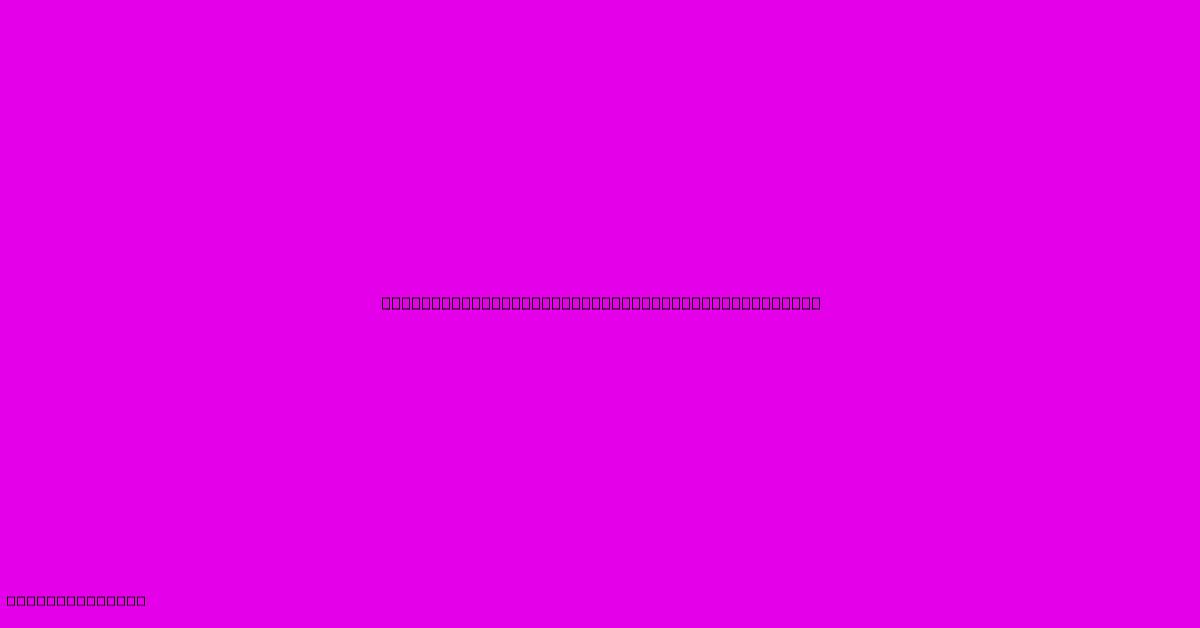
Thank you for visiting our website wich cover about Advanced Corrosion Technologies And Training. We hope the information provided has been useful to you. Feel free to contact us if you have any questions or need further assistance. See you next time and dont miss to bookmark.
Featured Posts
-
T5 7 Day Smart Wi Fi Programmable Thermostat With Geofence Technology
Jan 04, 2025
-
How Does Technology Influence Culture
Jan 04, 2025
-
Becs Technology Inc
Jan 04, 2025
-
Electrical Systems Technology
Jan 04, 2025
-
Dell Technologies Ovens
Jan 04, 2025