Abrasive Technologies
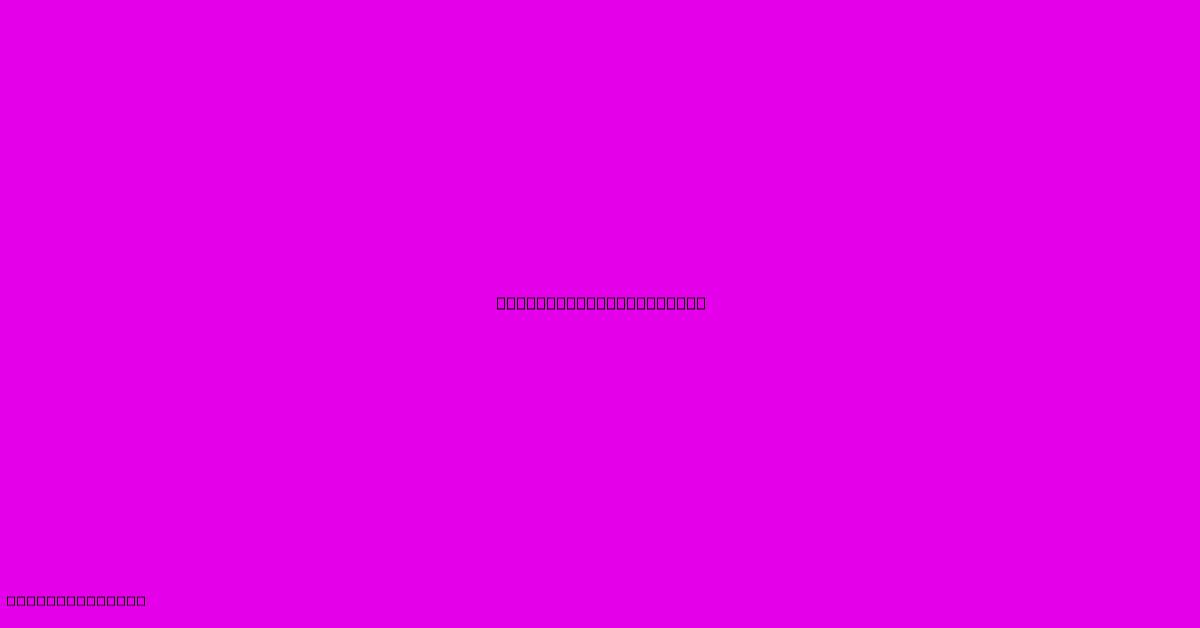
Discover more detailed and exciting information on our website. Click the link below to start your adventure: Visit Best Website mr.cleine.com. Don't miss out!
Table of Contents
Abrasive Technologies: Shaping Industries Through Precision and Power
Abrasive technologies encompass a broad range of processes and materials used to shape, finish, and clean various materials. From the delicate polishing of gemstones to the heavy-duty grinding of metal components, abrasive technologies play a crucial role across numerous industries. This article delves into the world of abrasive technologies, exploring their applications, the different types of abrasives used, and the advancements shaping the future of this critical field.
Understanding Abrasive Technologies
At its core, abrasive technology involves using hard, sharp particles to remove material from a workpiece. This material removal can be achieved through various methods, each tailored to specific needs and materials:
-
Grinding: This process uses rotating abrasive wheels or belts to remove material from a workpiece, creating a smooth or precise finish. Grinding is widely used in metalworking, manufacturing, and various other industrial applications.
-
Polishing: A finer form of abrasive material removal, polishing focuses on achieving a high-gloss finish. It's often the final step in a manufacturing process, enhancing the appearance and sometimes the performance of the product.
-
Lapping and Honing: These precision processes use extremely fine abrasives to achieve exceptionally smooth surfaces, often used in the production of highly precise components like engine parts or optical lenses.
-
Sandblasting: This process uses a high-velocity stream of abrasive particles (often sand or glass beads) to clean or etch surfaces. It's frequently used for surface preparation, cleaning, and decorative effects.
-
Ultrasonic Finishing: This relatively new method utilizes ultrasonic vibrations combined with abrasive slurries to achieve very fine surface finishes. It is particularly useful for intricate geometries and delicate parts.
Types of Abrasives
The effectiveness of an abrasive technology largely depends on the type of abrasive used. Common abrasive materials include:
-
Silicon Carbide (SiC): Known for its sharpness and hardness, SiC is widely used in grinding wheels and other abrasive tools.
-
Aluminum Oxide (Al2O3): Another popular choice, Al2O3 provides a good balance of hardness, toughness, and cost-effectiveness.
-
Cubic Boron Nitride (CBN): Extremely hard, CBN is used for machining hard materials like hardened steels and ceramics.
-
Diamond: The hardest known material, diamond abrasives are utilized for extremely demanding applications, such as cutting and polishing gemstones or superhard materials.
-
Ceramics: Engineered ceramic abrasives offer a wide range of properties depending on their composition, allowing for tailored solutions for specific applications.
Applications Across Industries
Abrasive technologies are essential across various sectors:
-
Automotive: Manufacturing engine components, body panels, and other parts.
-
Aerospace: Producing precision components for aircraft and spacecraft.
-
Medical: Creating implants, prosthetics, and surgical instruments.
-
Electronics: Manufacturing semiconductors and other precision components.
-
Construction: Cutting, shaping, and finishing building materials.
-
Jewelry and Gemstone Industry: Cutting, polishing, and shaping precious stones.
Advancements in Abrasive Technologies
The field of abrasive technologies is constantly evolving, with ongoing research and development leading to several advancements:
-
Nanomaterials: The use of nanomaterials in abrasives enhances their performance by improving hardness, sharpness, and durability.
-
Advanced Coatings: Applying specialized coatings to abrasive tools improves their wear resistance and performance.
-
Automation and Robotics: Integrating abrasive processes with automated systems enhances efficiency and precision.
-
Sustainable Abrasives: The development of environmentally friendly abrasives reduces the environmental impact of abrasive technologies.
Conclusion
Abrasive technologies are fundamental to a wide array of manufacturing processes and industries. The continuous development of new materials, processes, and automation techniques promises further advancements, increasing efficiency, precision, and sustainability in the years to come. Understanding the principles and applications of abrasive technologies is crucial for anyone involved in manufacturing, engineering, or related fields.
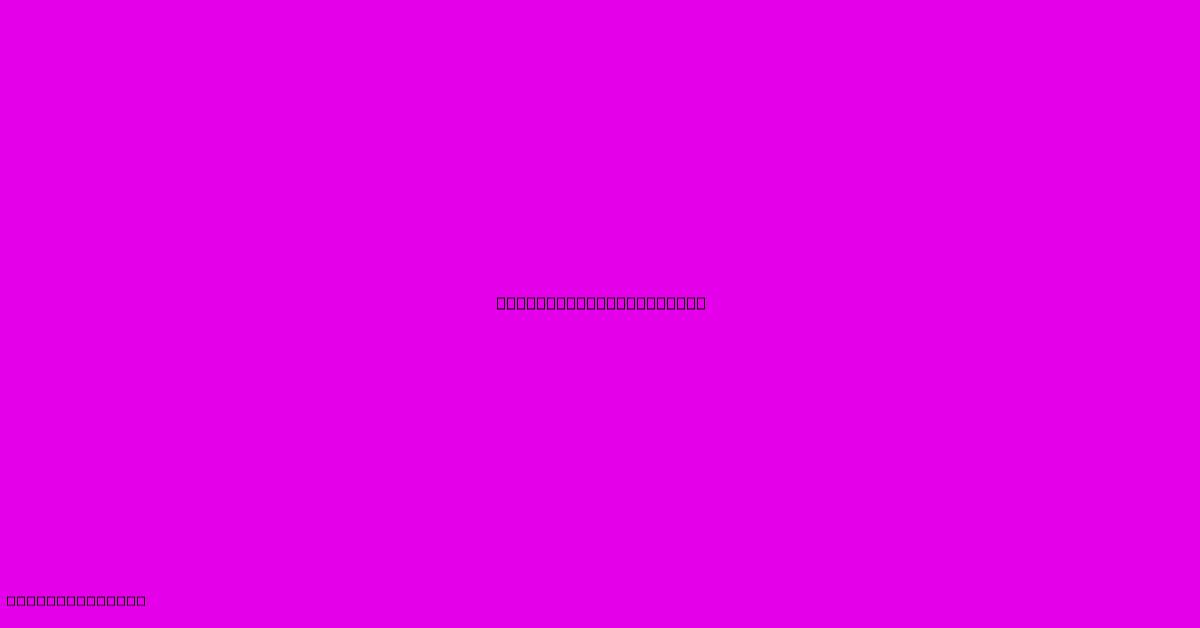
Thank you for visiting our website wich cover about Abrasive Technologies. We hope the information provided has been useful to you. Feel free to contact us if you have any questions or need further assistance. See you next time and dont miss to bookmark.
Featured Posts
-
Bangun Backlink Dapatkan Backlink Dari Situs Web Lain Yang Kredibel Dan Relevan Backlink Membantu Meningkatkan Otoritas Domain Anda Dan Meningkatkan Peringkat Pencarian Anda Berbagi Artikel Anda Di Media Sosial Juga Dapat Membantu Meningkatkan Visibilitas Anda
Dec 26, 2024
-
Ceos Technologies
Dec 26, 2024
-
Texans Game Channel Christmas 2024
Dec 26, 2024
-
Suns Avenge Loss Durant Beal Lead Win
Dec 26, 2024
-
Mid America Technology Center
Dec 26, 2024